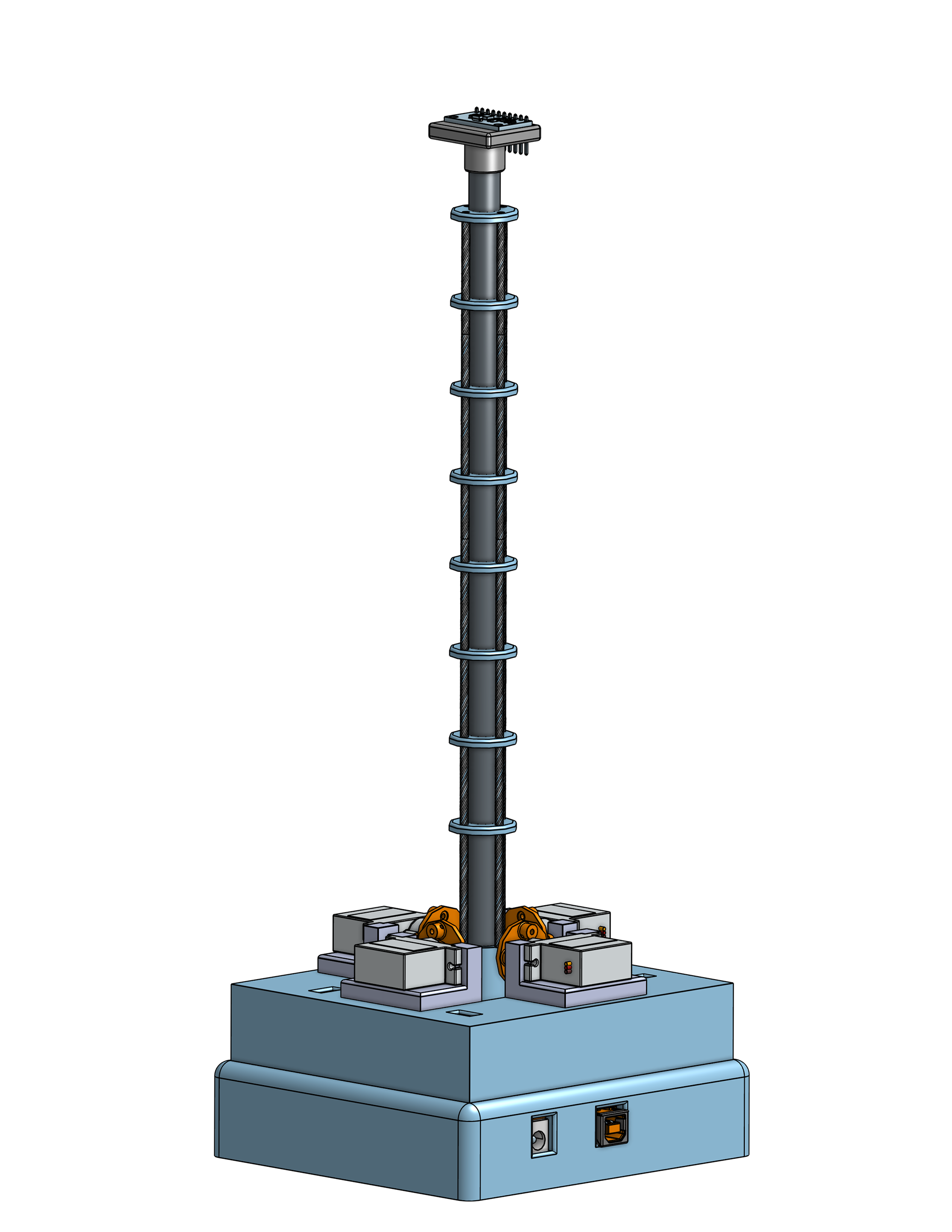
This project involved the design and fabrication of a tendon-driven continuum robot. It features a soft backbone, 3-D printed in TPU, and a series of vertebrae. The objective was to assess the feasibility of this design methodology for use in minimally-invasive robotic surgical procedures. I was responsible for the electromechanical design (from concept to CAD and implementation) and fabrication.
Design
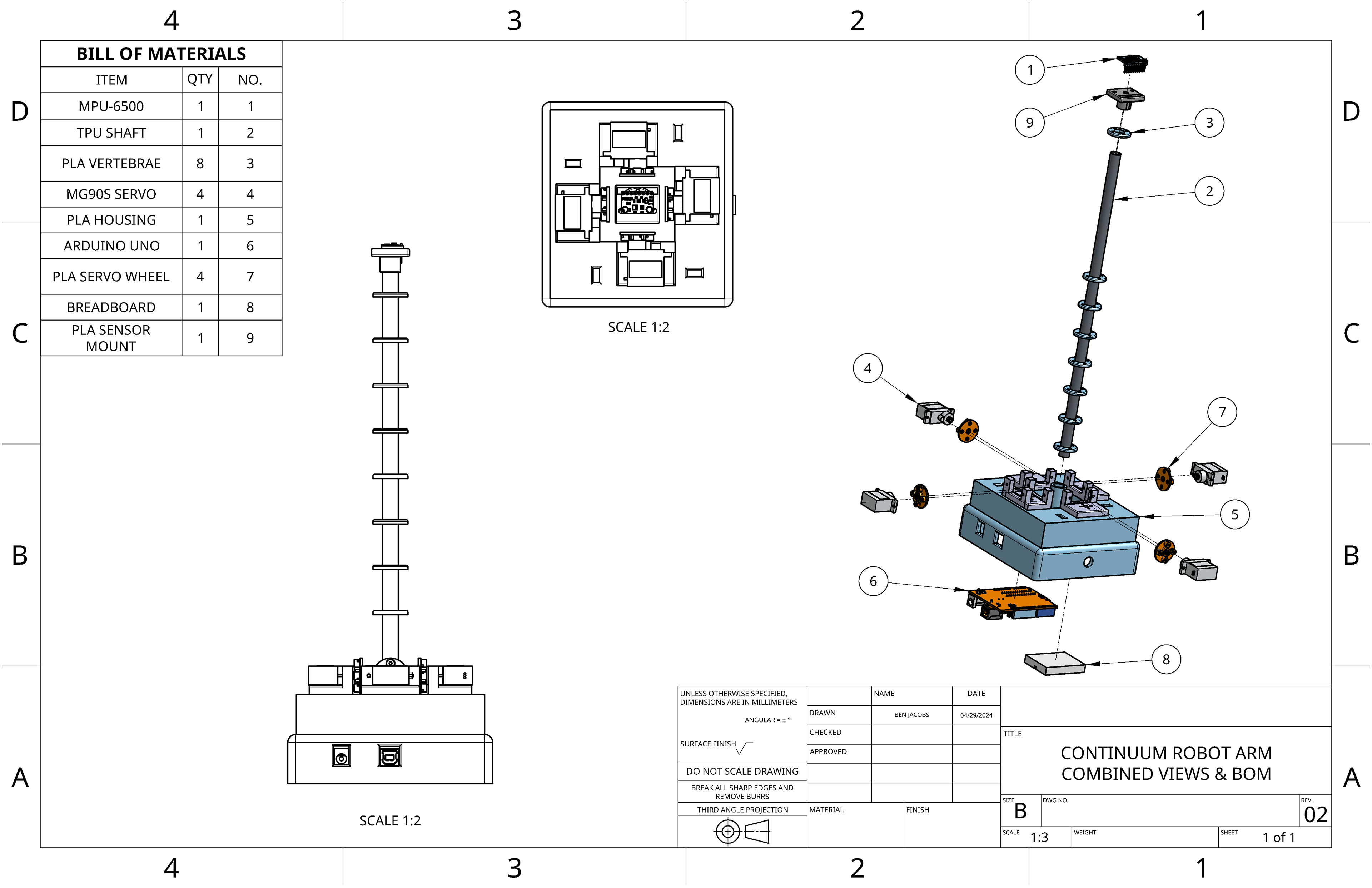
Exploded drawing view of assembly, featuring PLA enclosure and vertebrae, TPU shaft, 4 MG90s servos, Arduino board, and MPU-9250 6-axis gyroscope for sensing and positioning of end-effector.
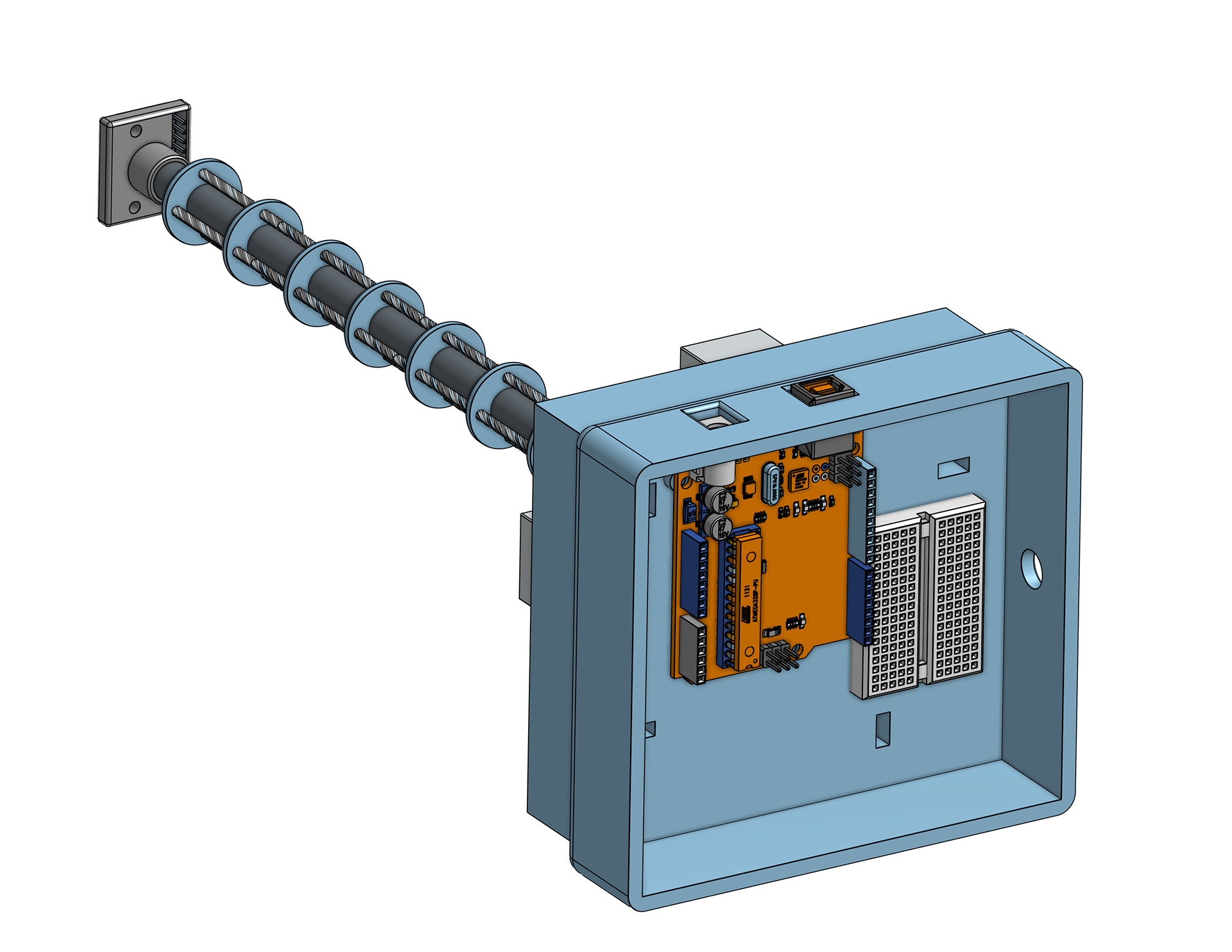
CAD rendering showing mounting of control board, cable routing channels, and power/data ports.
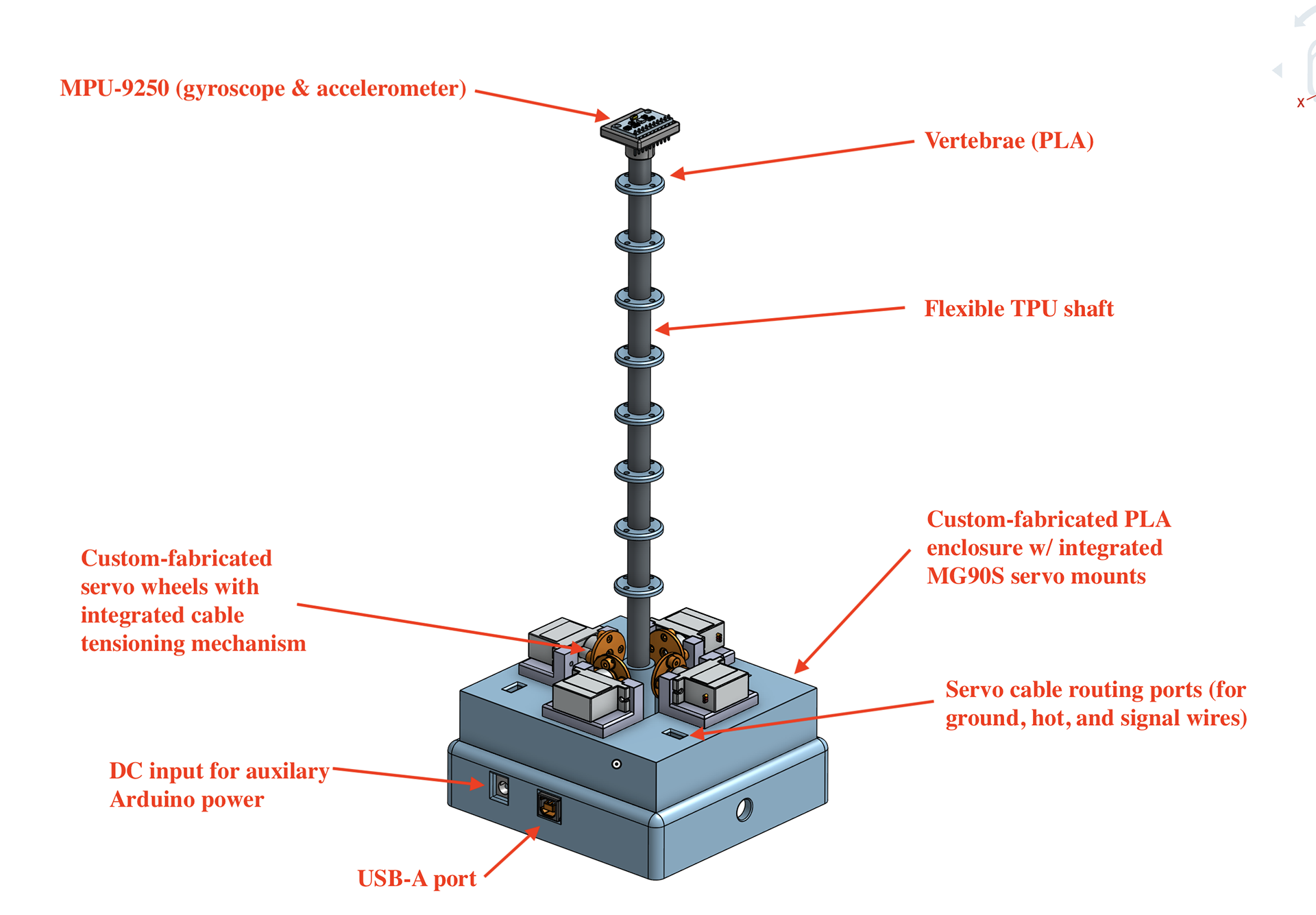
Labeled diagram with callouts to main components and features. The materials for all 3D-printed components are also specified.
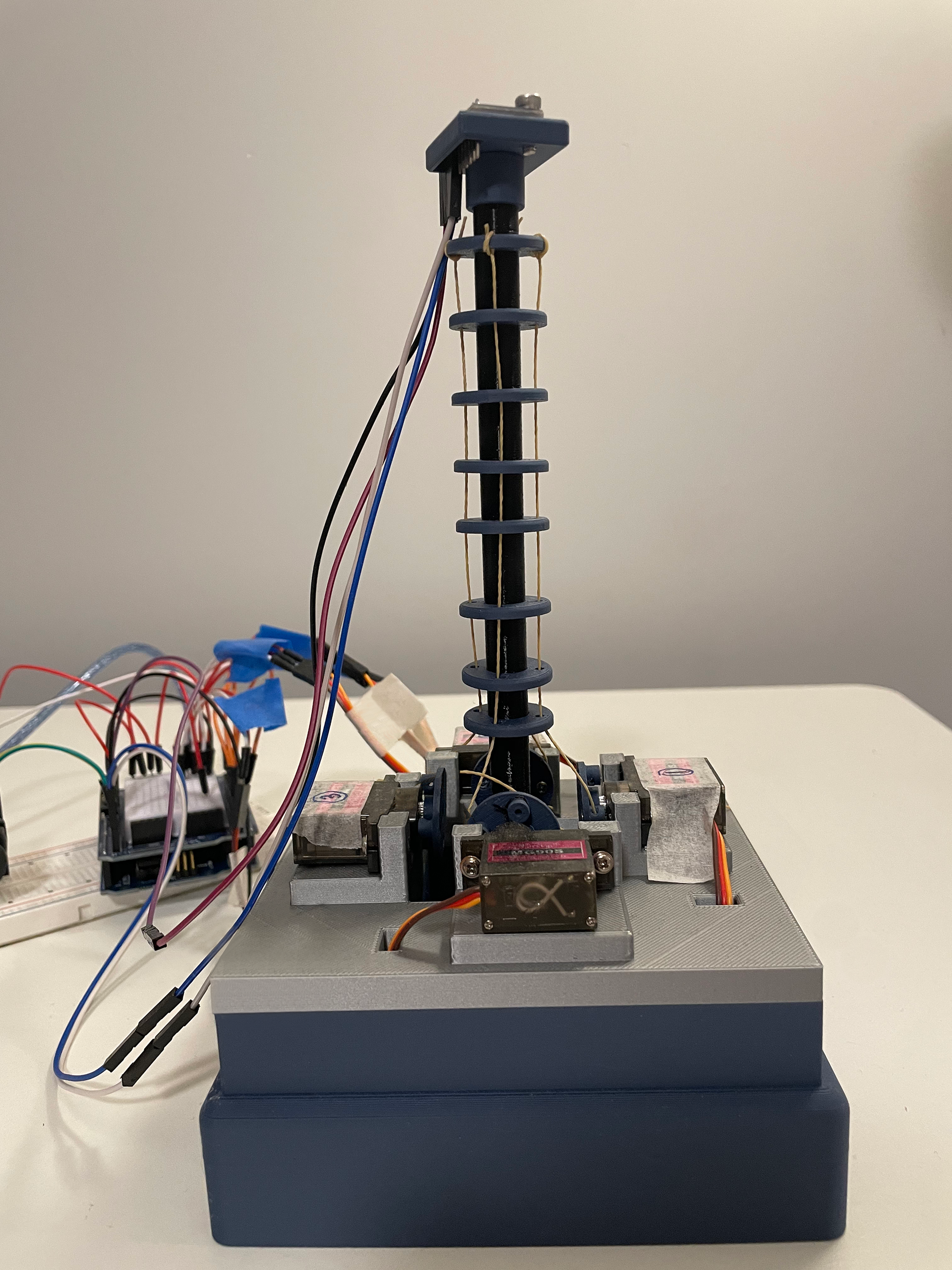
Fully-fabricated device.
Fabrication
Time-lapse video of 3D printing PLA components.
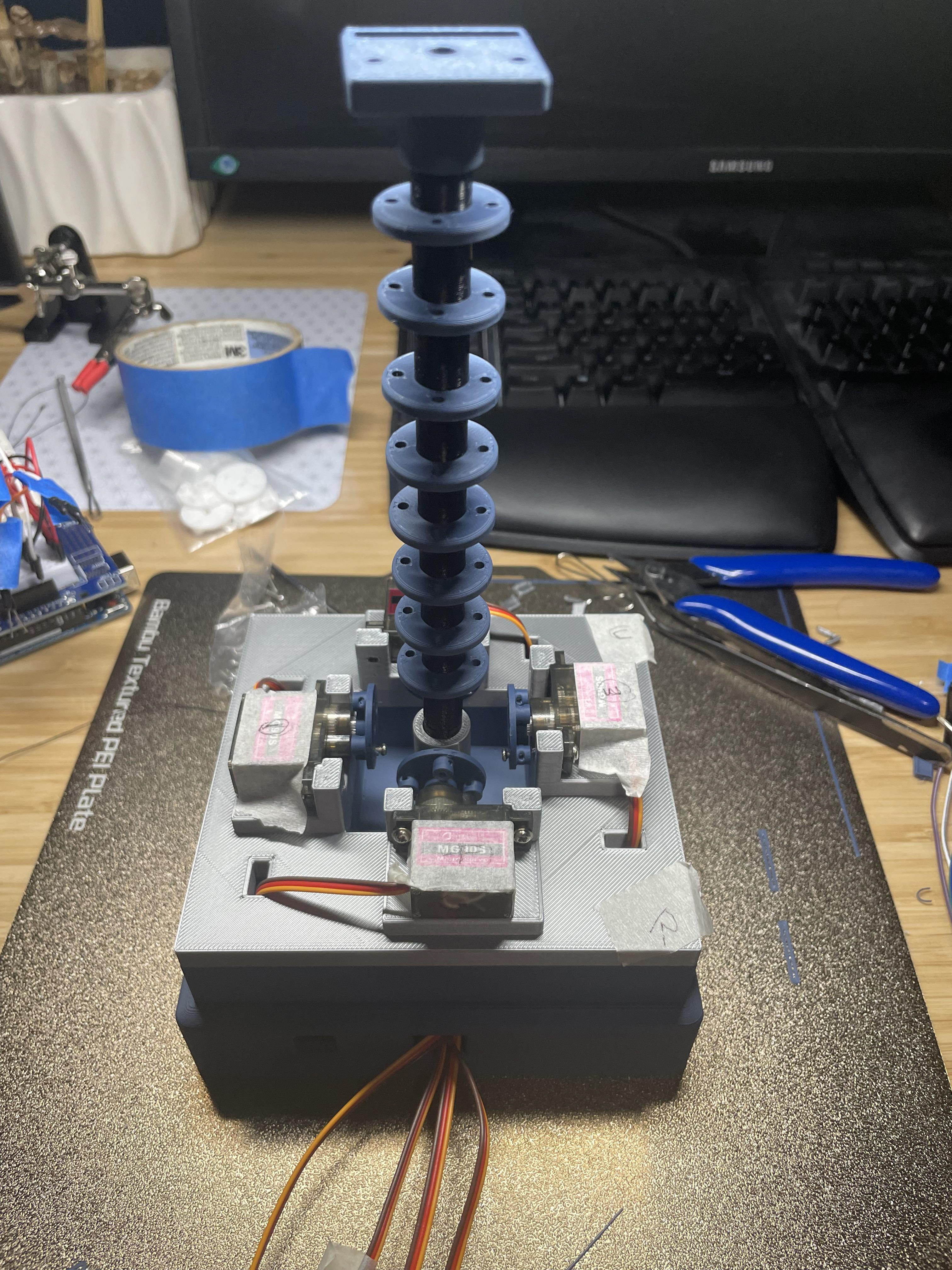
Initial assembly of electromechanical system on bench.
This project underscores the utility of FDM 3-D printing for rapid prototyping, testing, and design iteration. It also highlights how flexible filaments (in this case TPU) can be used to fabricate compliant materials, in combination with rigid materials such as PLA and PETG.
Operation
Video of completed platform in operation, showing active positional feedback on the serial monitor from the MPU-9250 gyroscope, and joystick control system.
The completed robot fulfilled all initial design objectives, and was able to reliably position the distal end of the backbone (end-effector) with both precision and accuracy.
Analysis
Due to the theoretically infinite degrees of freedom afforded by this continuum robot arm, it's behavior is best modeled via constant curvature modeling (CCM). Preliminary tests show that a CCM-driven framework would reliably capture the observed kinematic behavior of the system.
The final research paper for this project can be accessed below. This report includes a thorough review of the existing state of the art for minimally-invasive surgical robots, and presents the results of NASA task-load testing performed with the robot, to quantify the reduced mental exertion on human operators, relative to manual operation of conventional endoscopes.