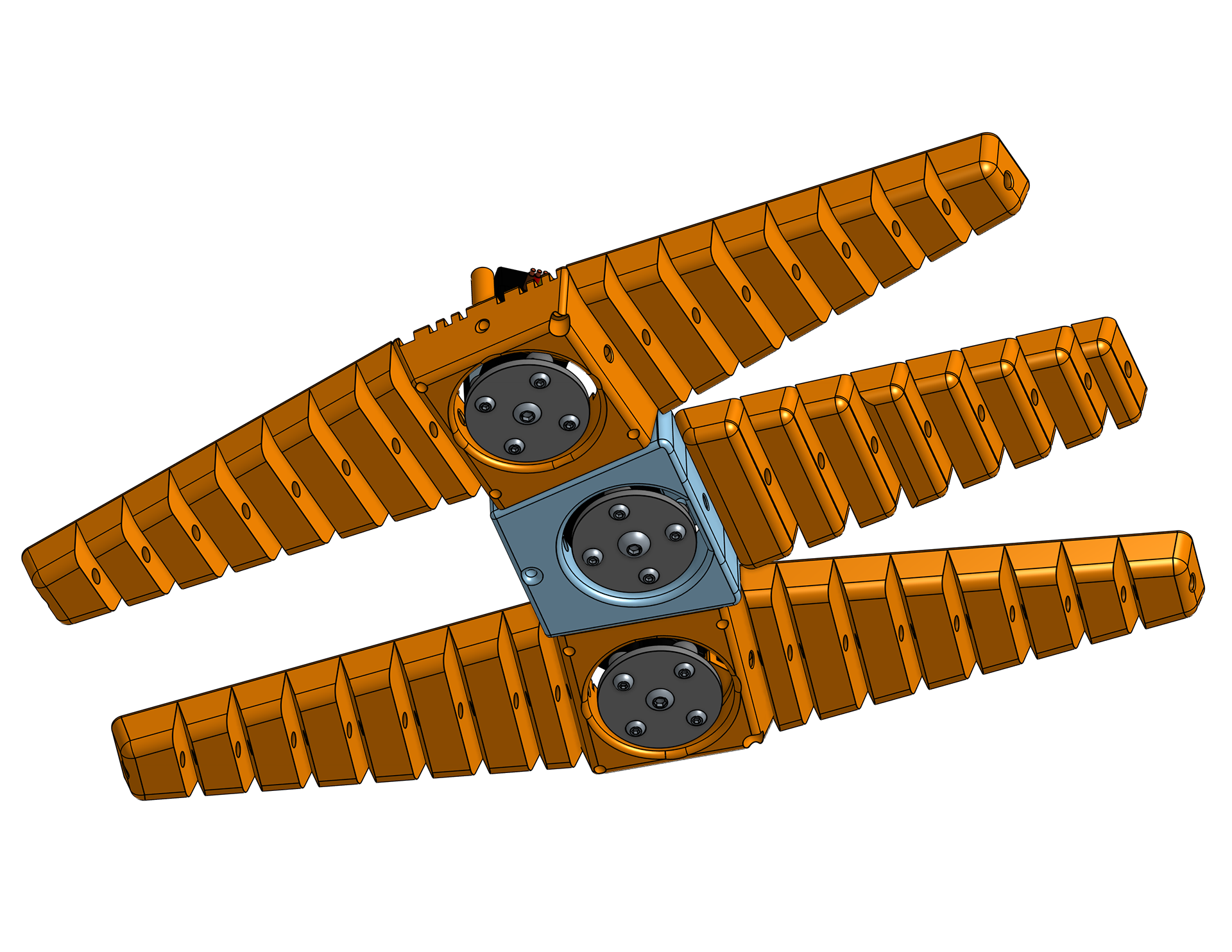
Full CAD rendering of final design (bottom perspective).
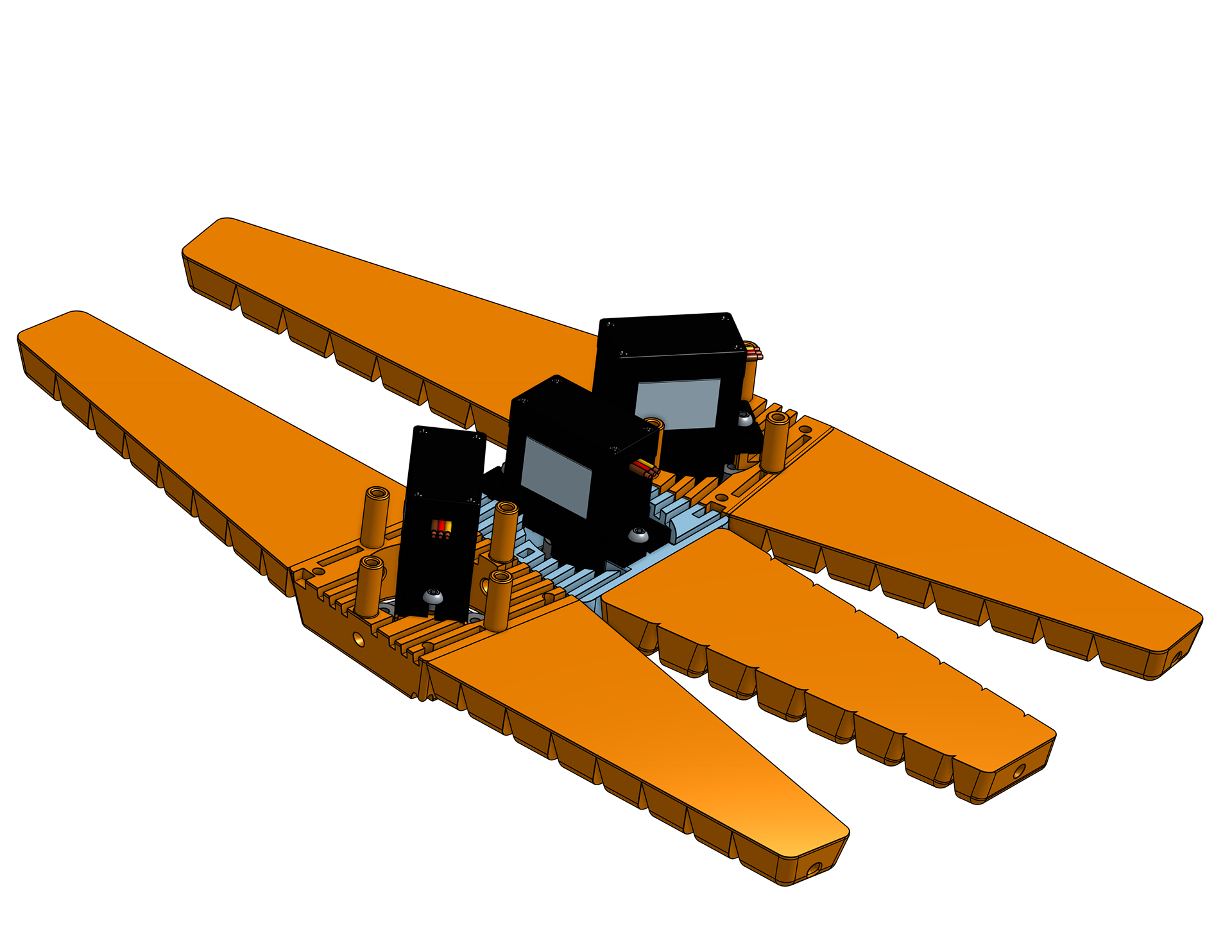
Full CAD rendering of final design (top perspective).
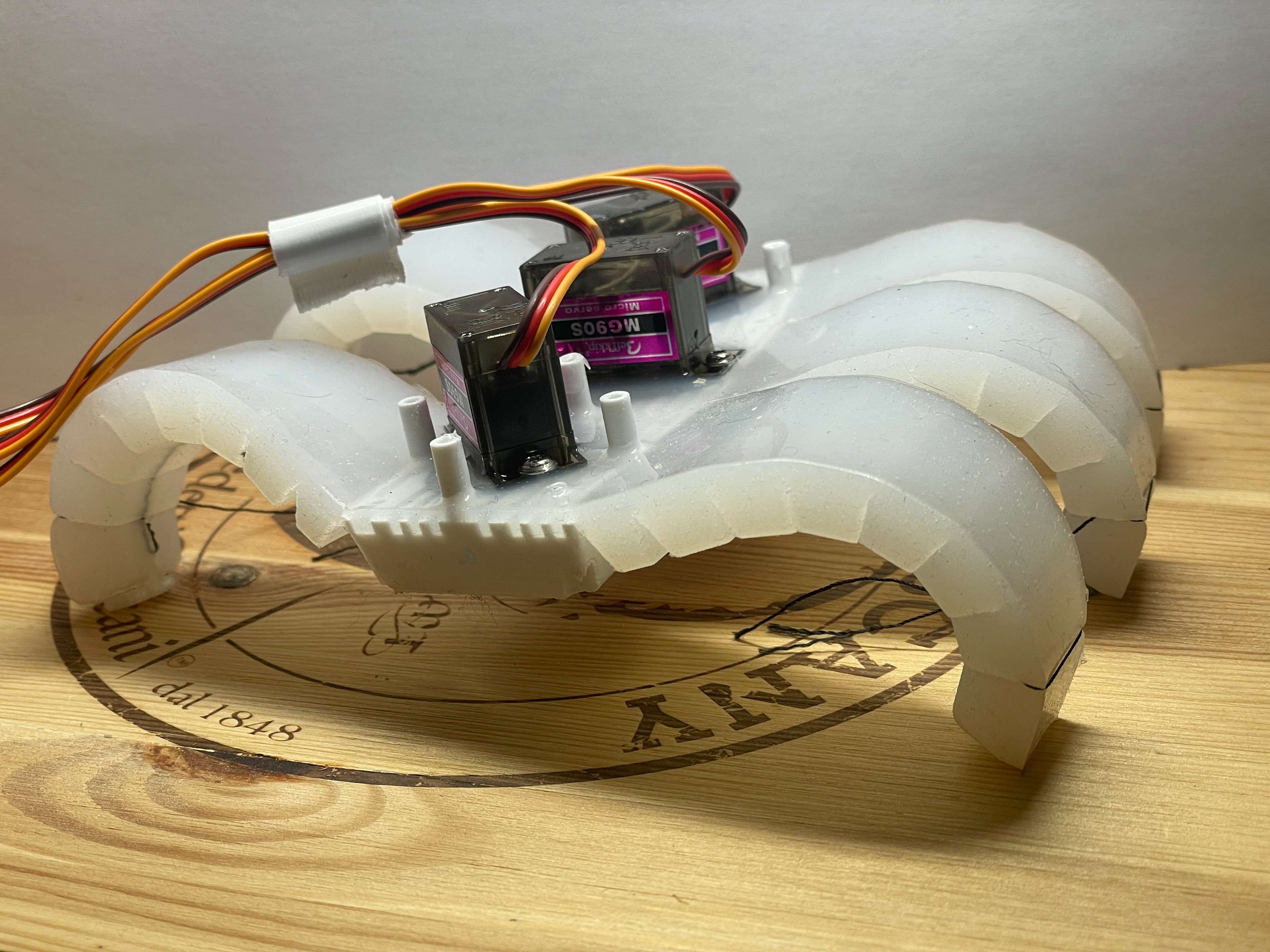
Fully-fabricated assembly, showing the robot's ability to stand upright and support its own weight without any buckling of the soft silicone legs.
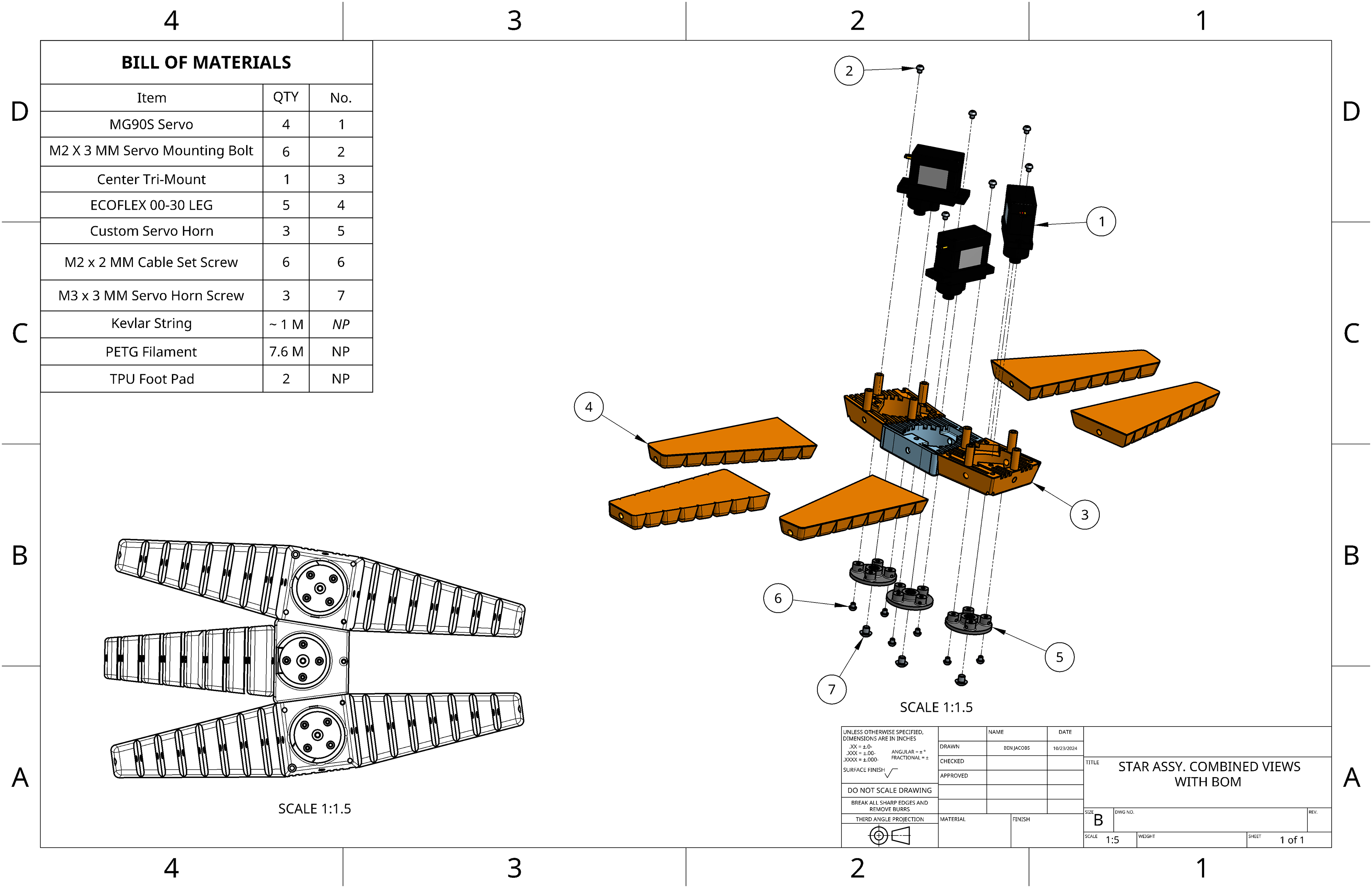
Exploded drawing view of final Starfish soft robot design. Featuring 3 MG90s metal-geared servos, with silicone (Ecoflex 00-30) limbs and PETG torso. Full components detailed in BOM.
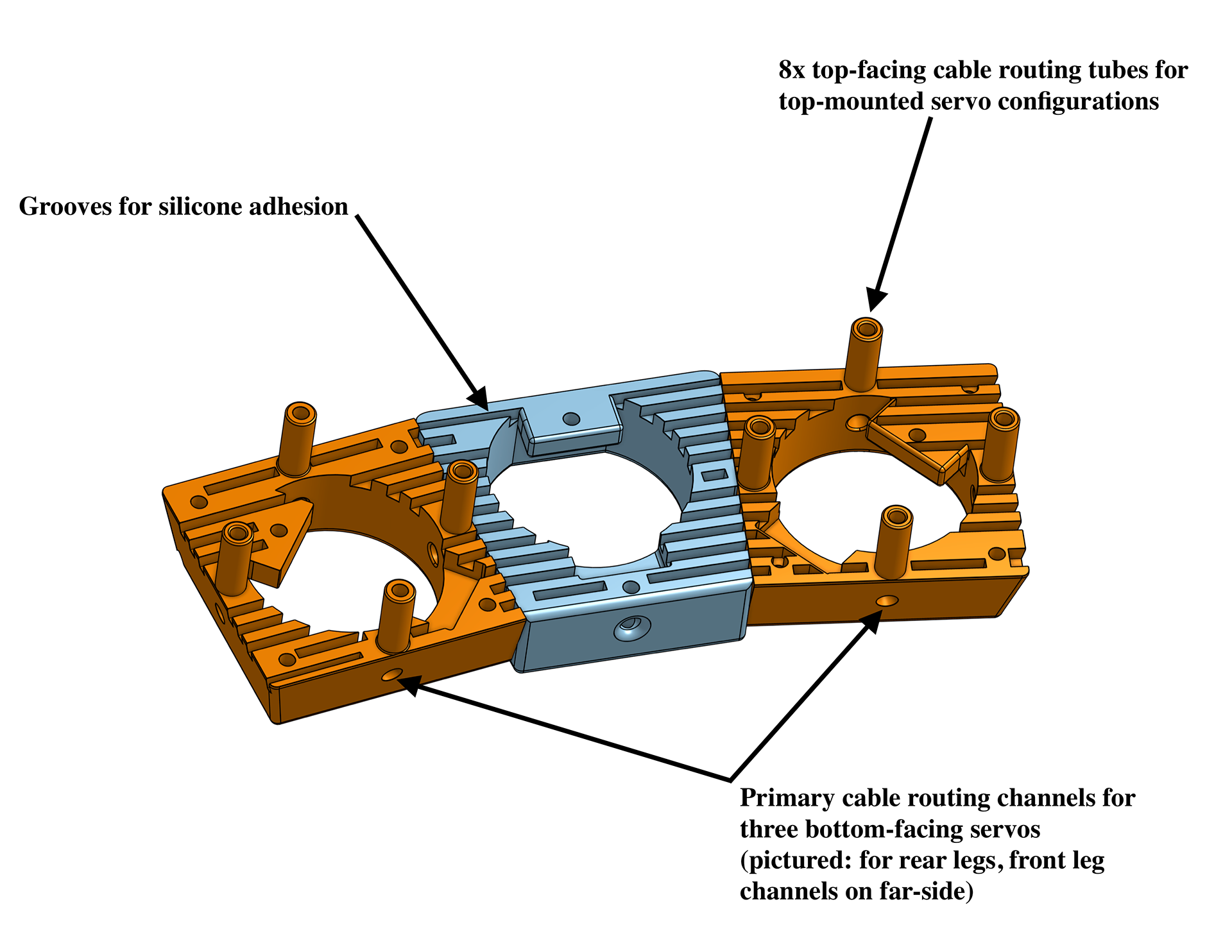
CAD rendering Tri-hub component, which was 3D-printed in PETG for durability and ease of threading fasteners. The hubs top face has grooves which maximize adhesion of silicone to the part. The channels were designed to minimize friction, and maximize transfer of mechanical energy during tensioning.
This final design was the product of many iterative prototypes.
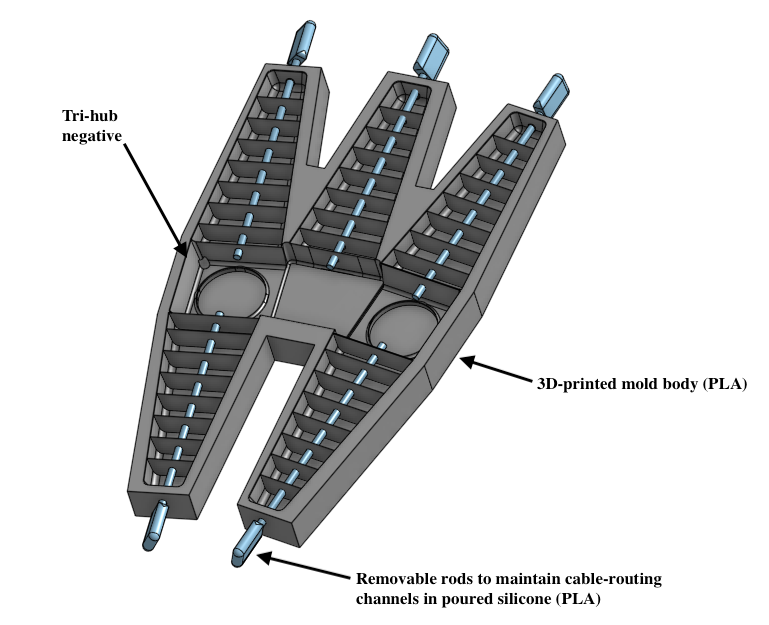
Diagram of silicone mold with key features labeled.
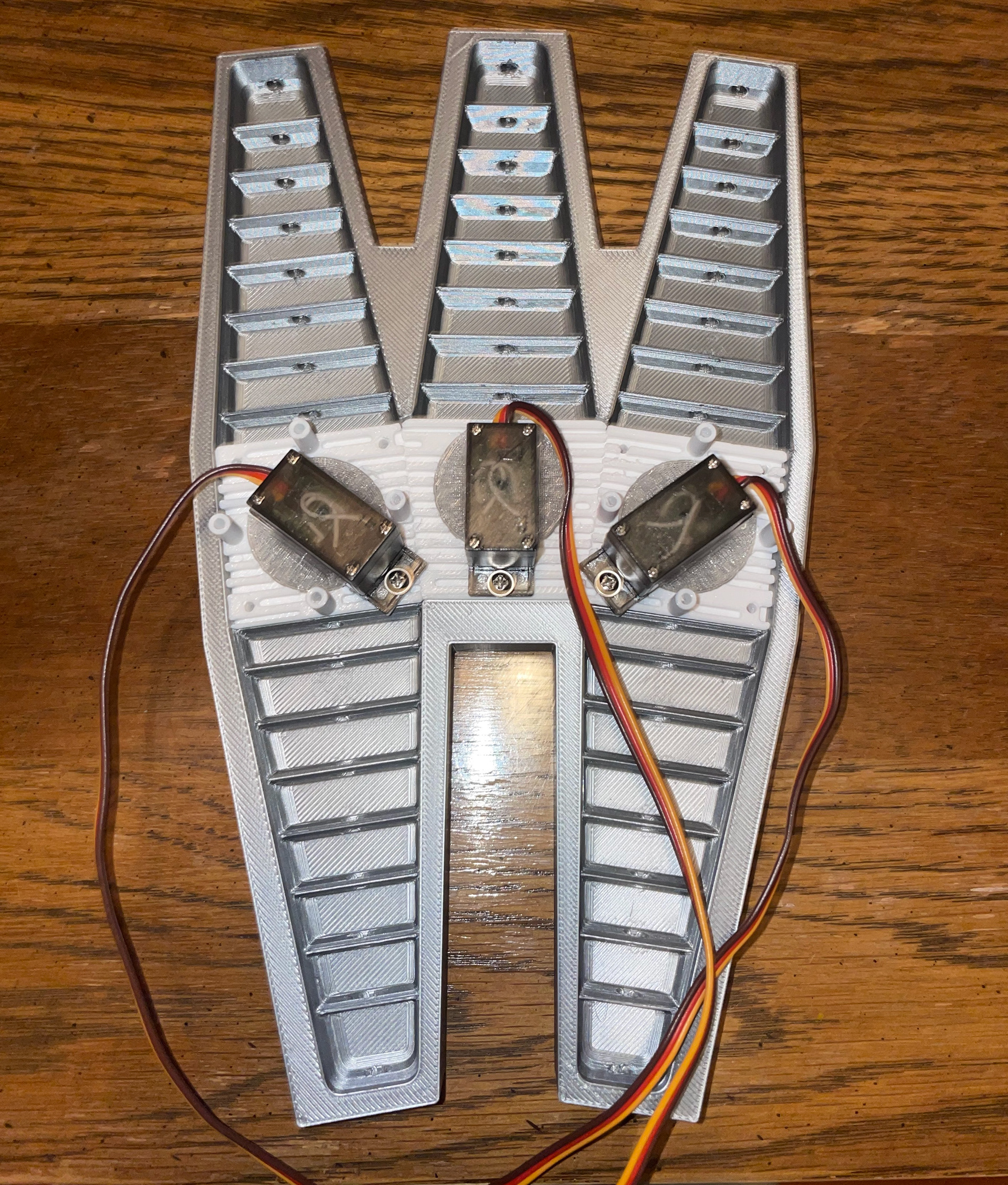
Completed mold with Tri-hub and servos fully seated; ready for silicone pouring.
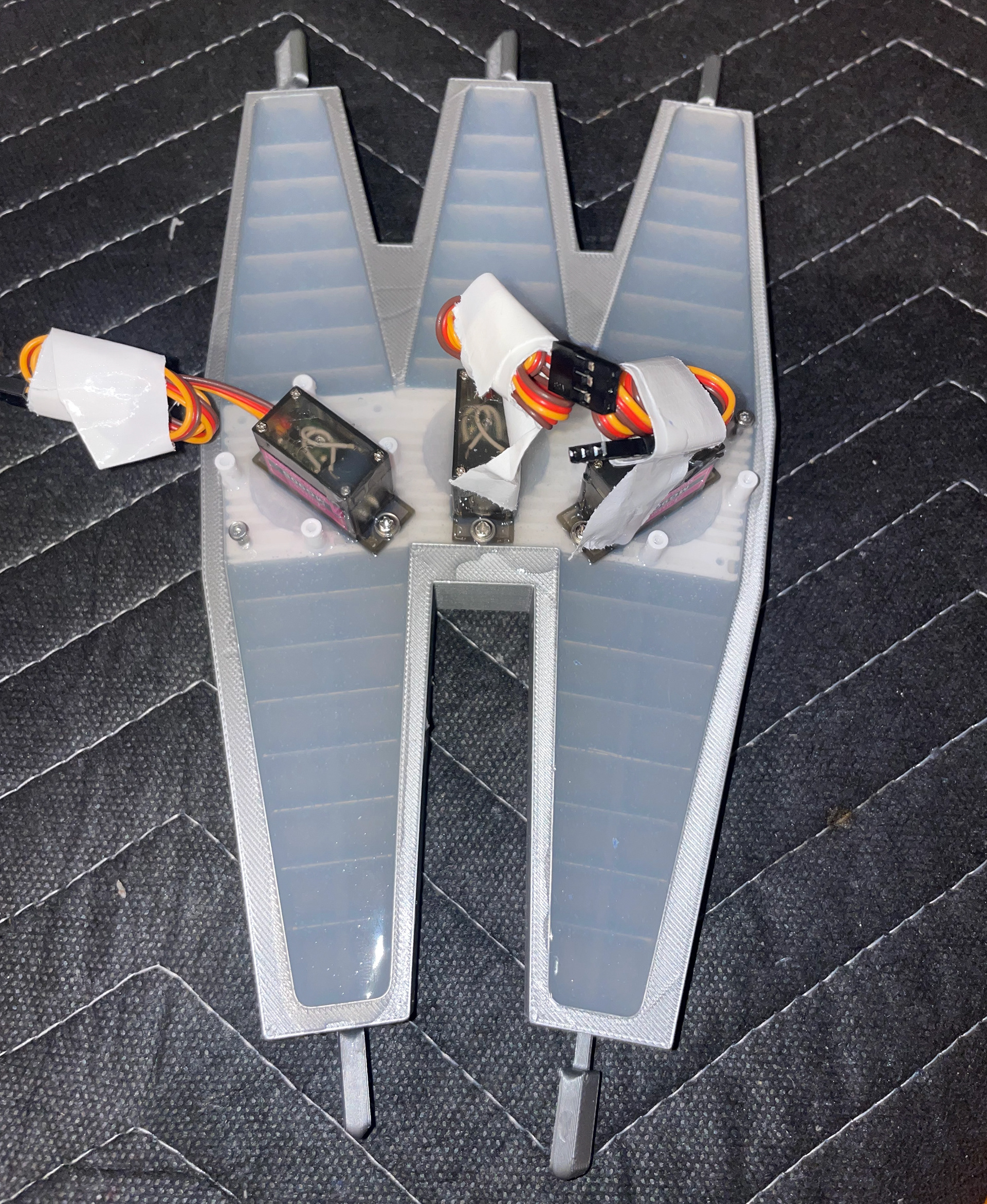
Mold filled with curing silicone.
Demo video of final operational robot featuring initial bench tests to validate both electromechanical control and forward, left, and right maneuvering capabilities.
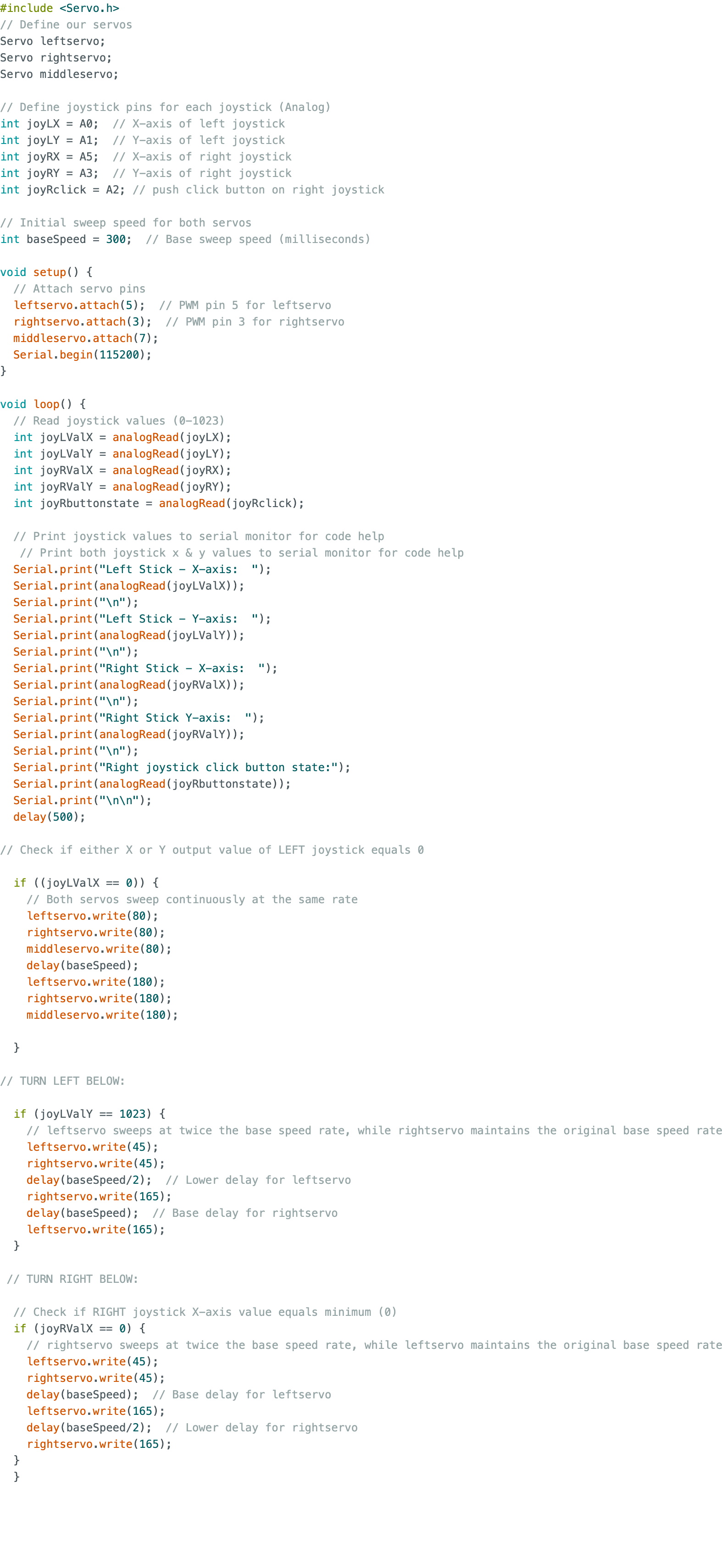
C++ code for real-time control of all three servo's using pair of two-axis joysticks.
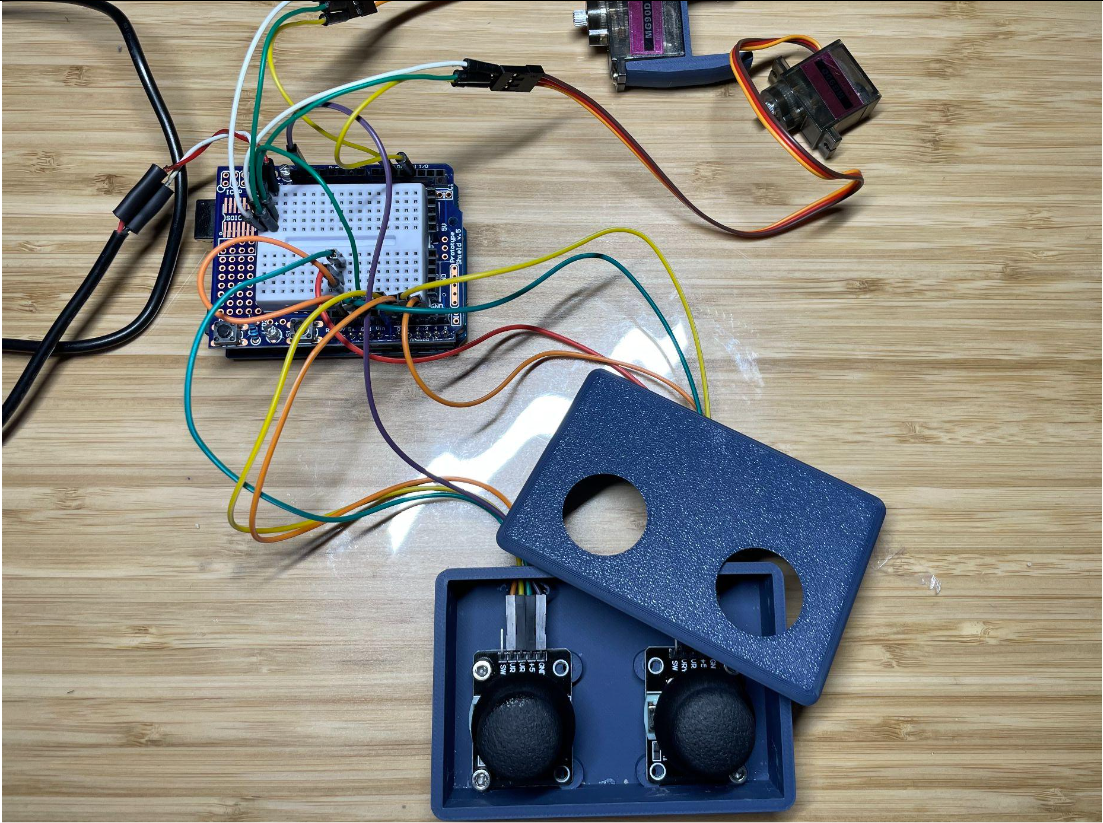
Demo set up of 3D-printed joystick enclosure and prototyping board with servo wiring and DC power input.