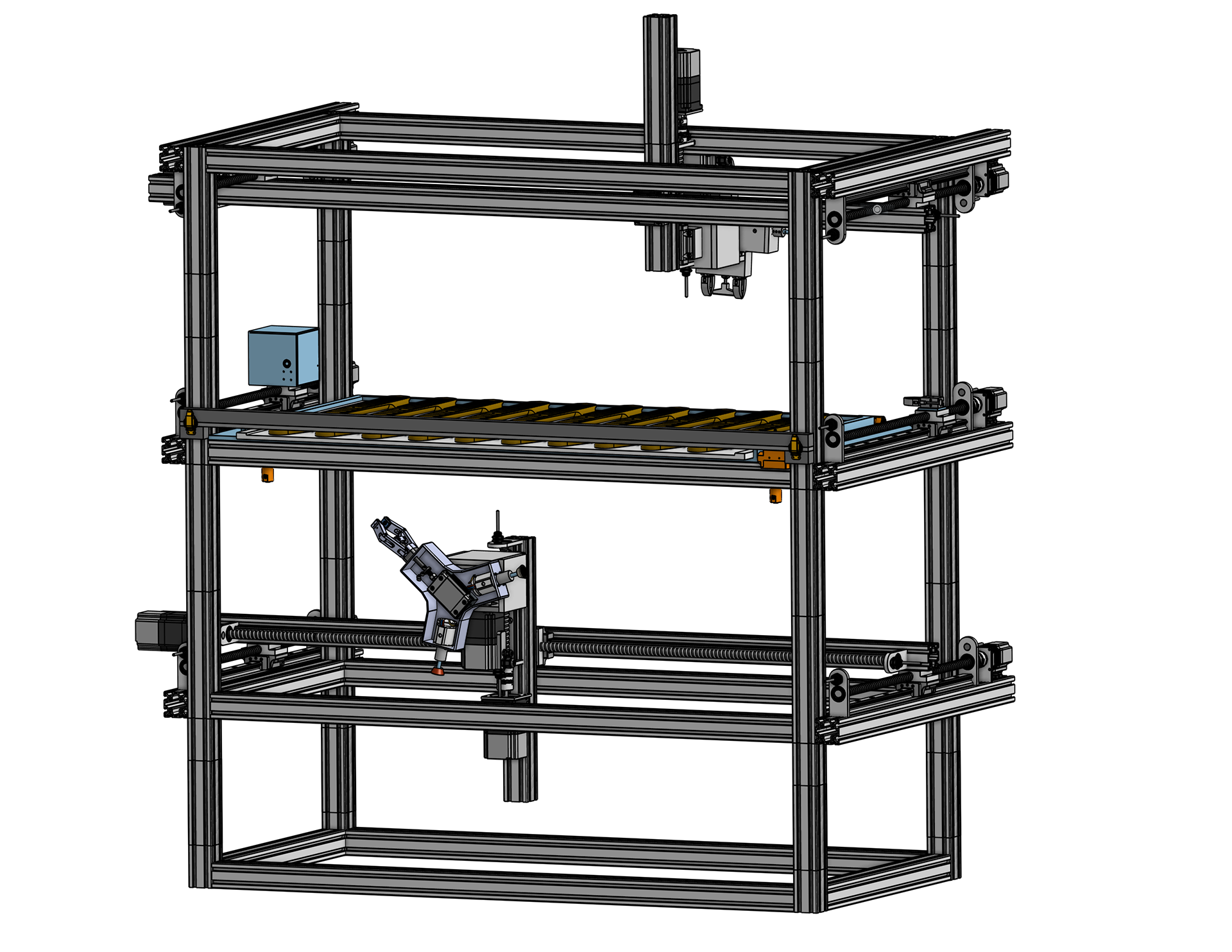
Isometric system view of the GFM-57 (guitar fretting machine).
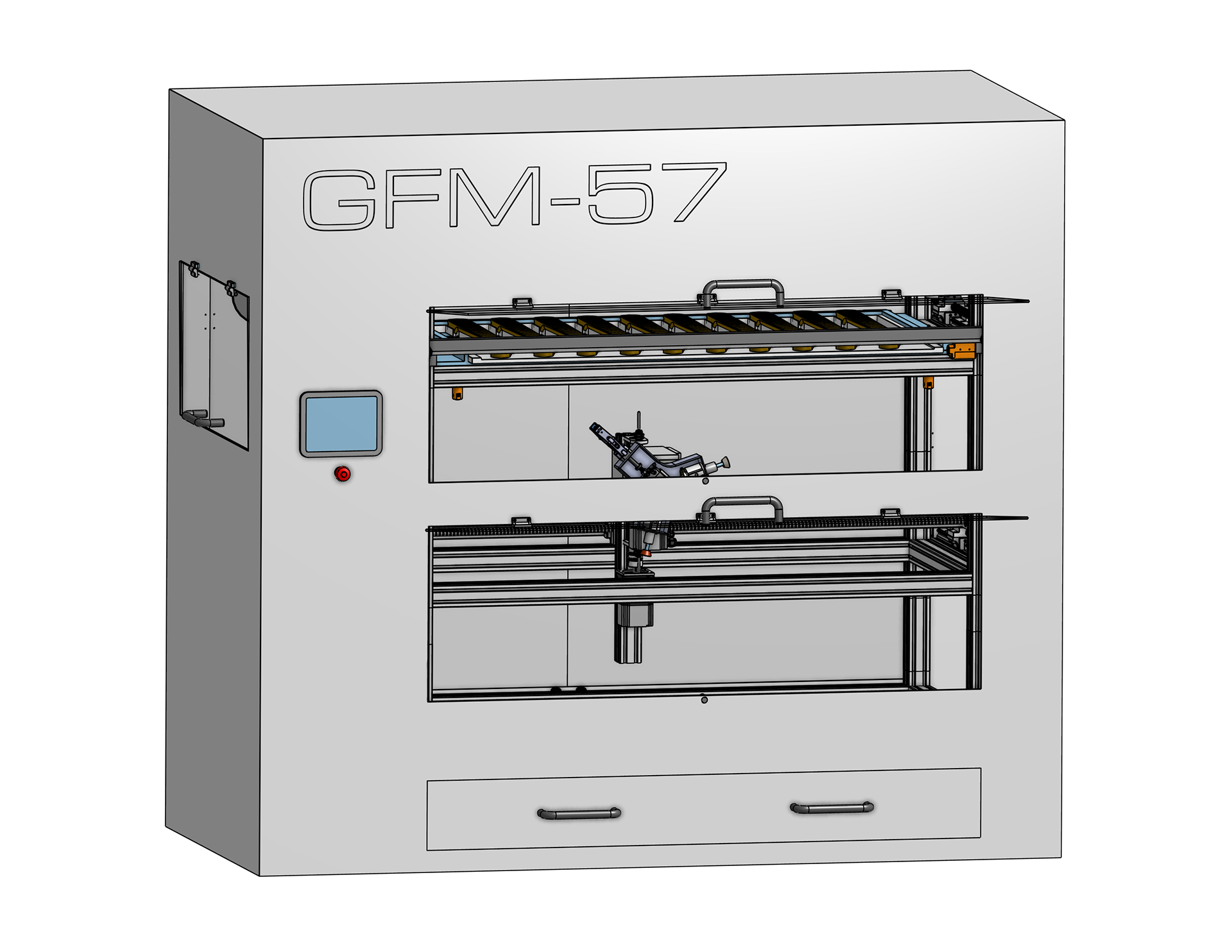
System view with housing, including user display, access windows and waste bin.
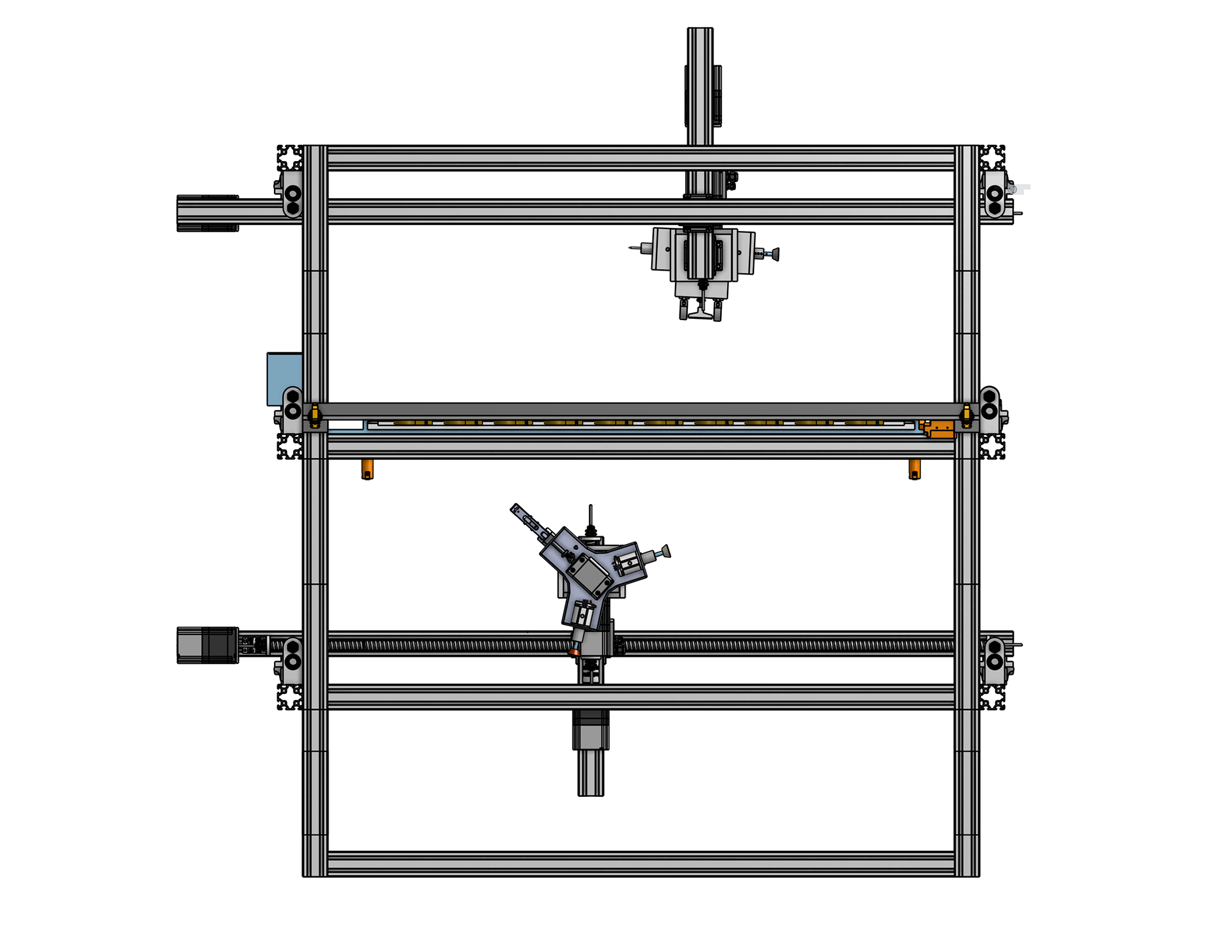
System profile view depicting the bottom tool wheel (BTW), which performs fret wire cutting, grinding, and polishing.
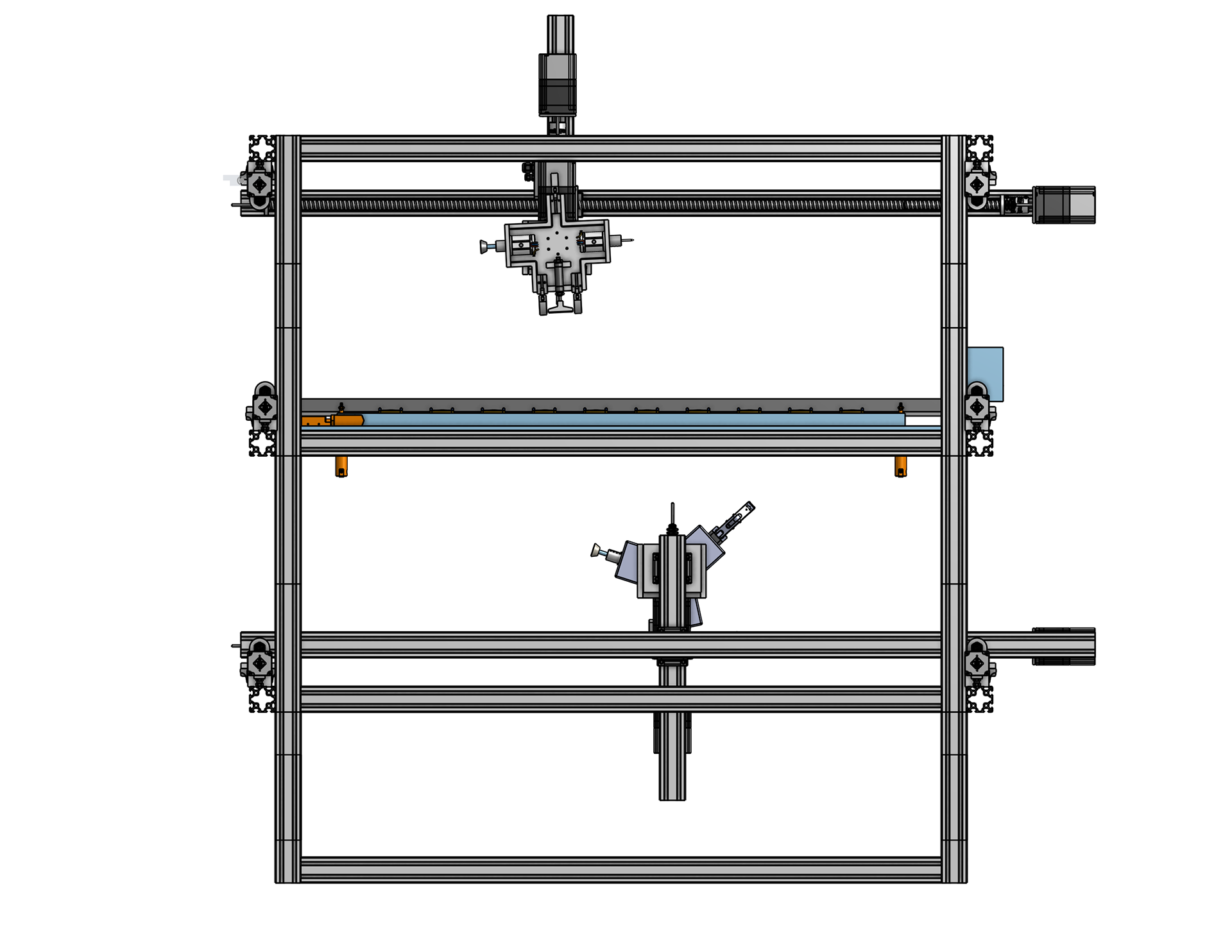
System profile view depicting the top tool wheel (TTW), which performs fret slot milling, fret pressing, fret grinding (in tandem with the BTW), and fret wire feeding to the eater-feeder subsystem, detailed below.
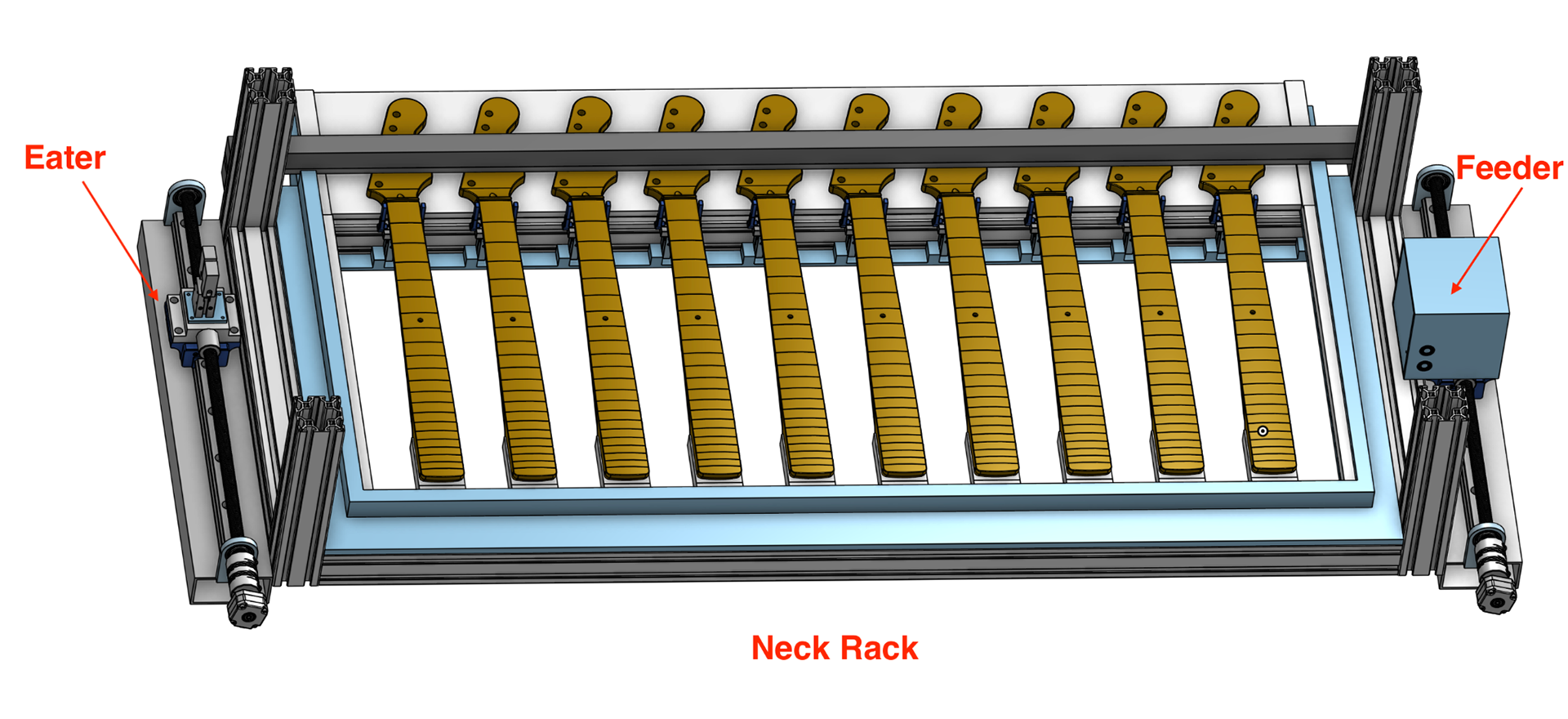
Subsystem view of the neck rack and Eater-Feeder mechanism, the latter of which is detailed in the below diagram.
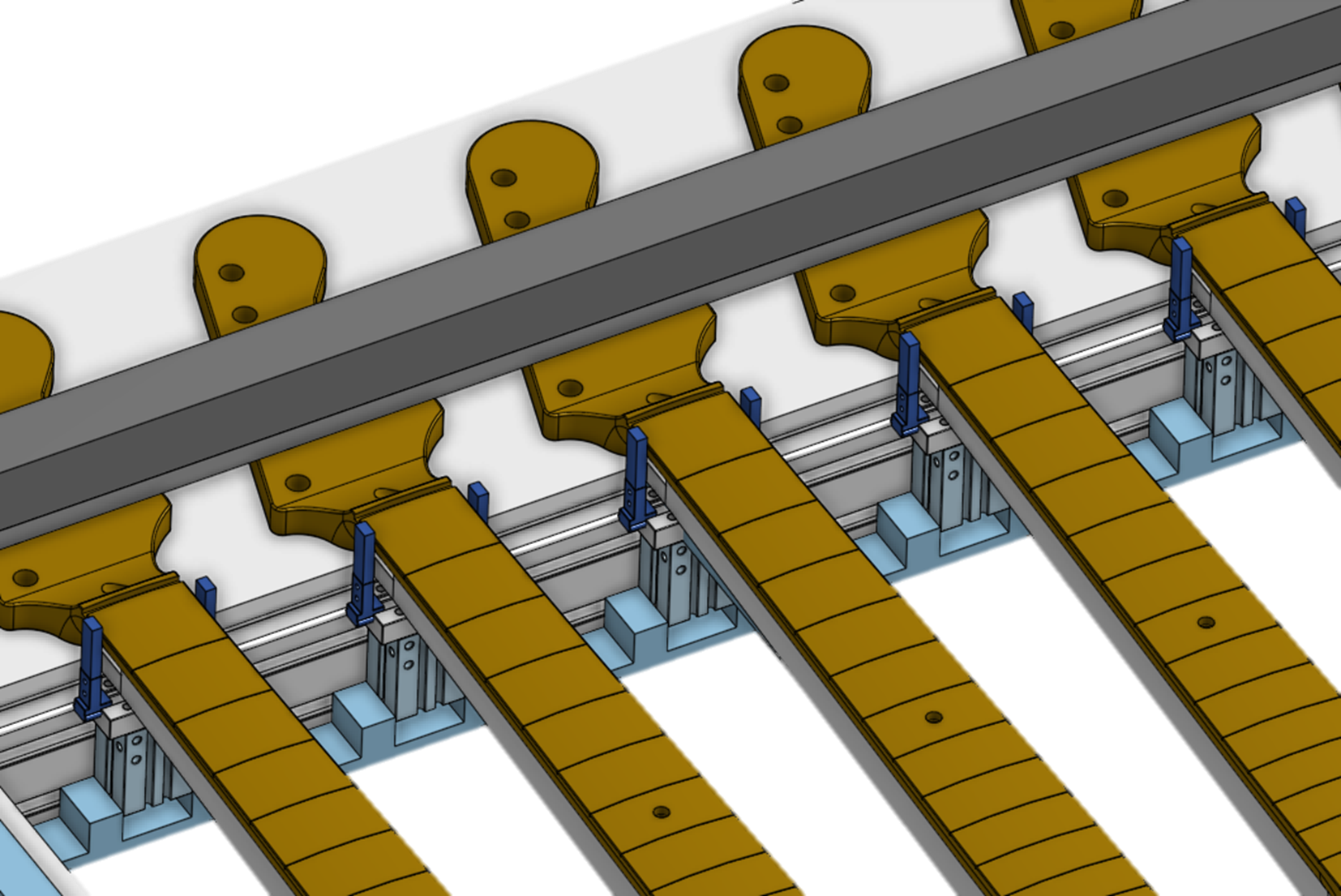
The neck rack uses pneumatic grippers (blue) to secure each neck laterally. These allow for necks of varying radii and fret widths to be secured by one universal mechanism. A retaining bar (grey) is used to fix the necks vertically.
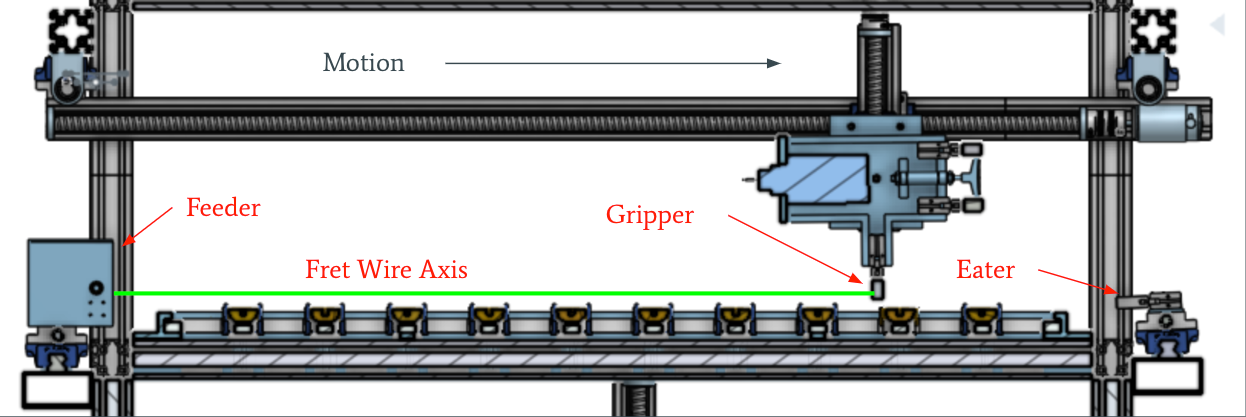
The Eater-Feeder subsystem dispenses, aligns, and presses the fret wire for each of the 24 rows of frets. It consists of three primary components:
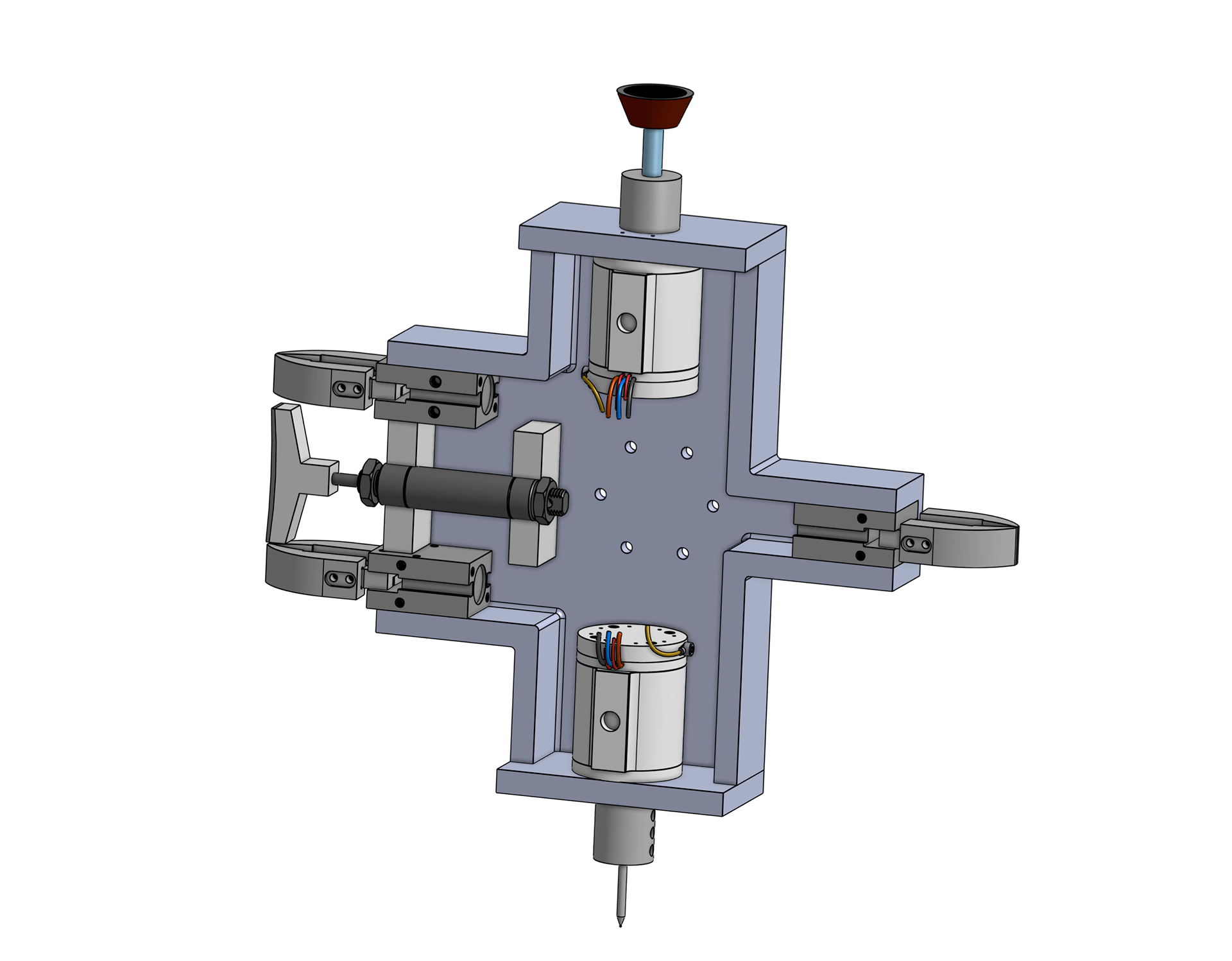
The Top Tool Wheel (T.T.W.) performs fret slot milling (bottom), fret wire handoff to the Eater (right), fret wire pressing (left), and fret grinding (top).
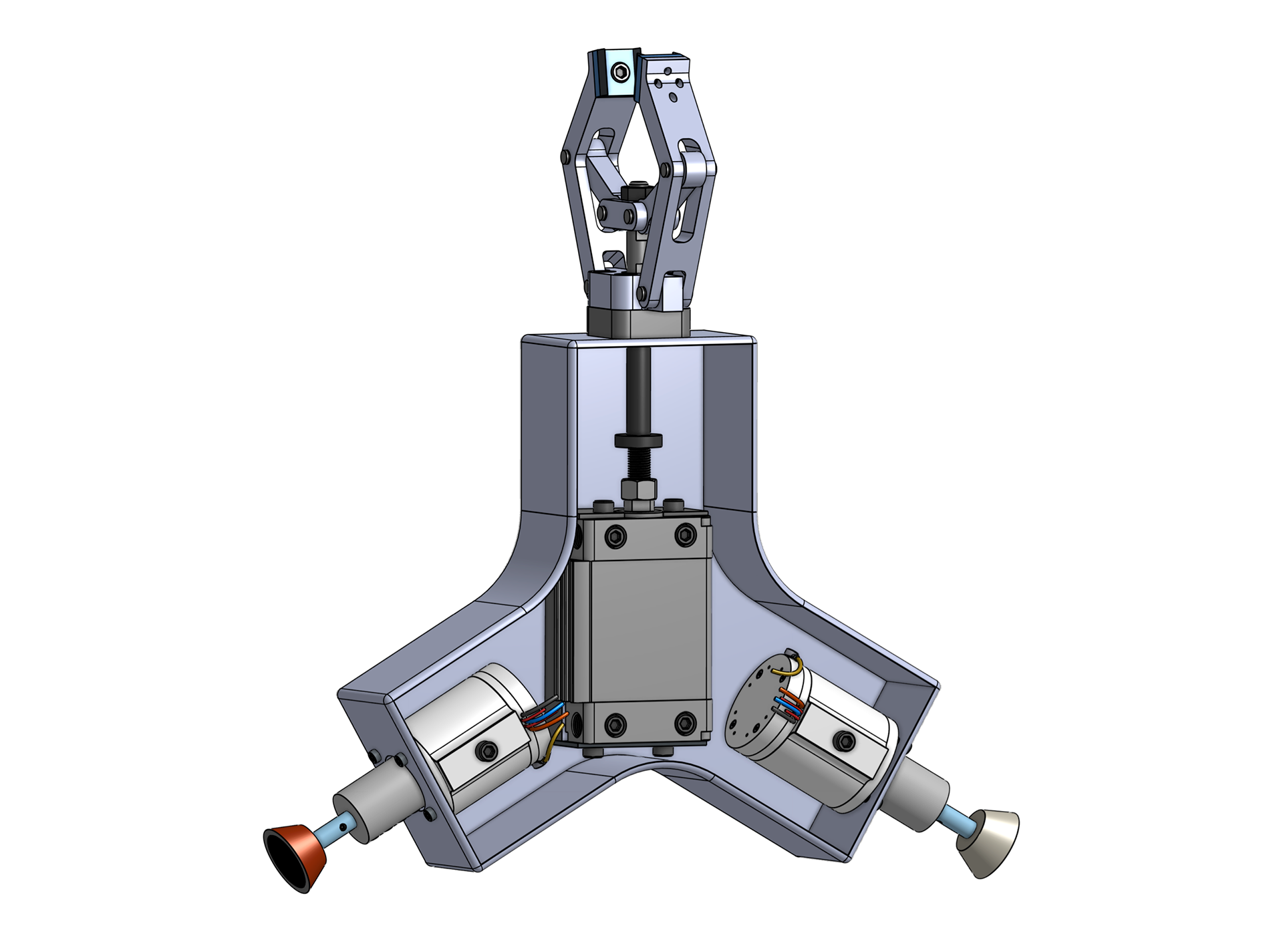
The Bottom Tool Wheel (B.T.W.) performs fret cutting (top), grinding (left), and polishing (right).
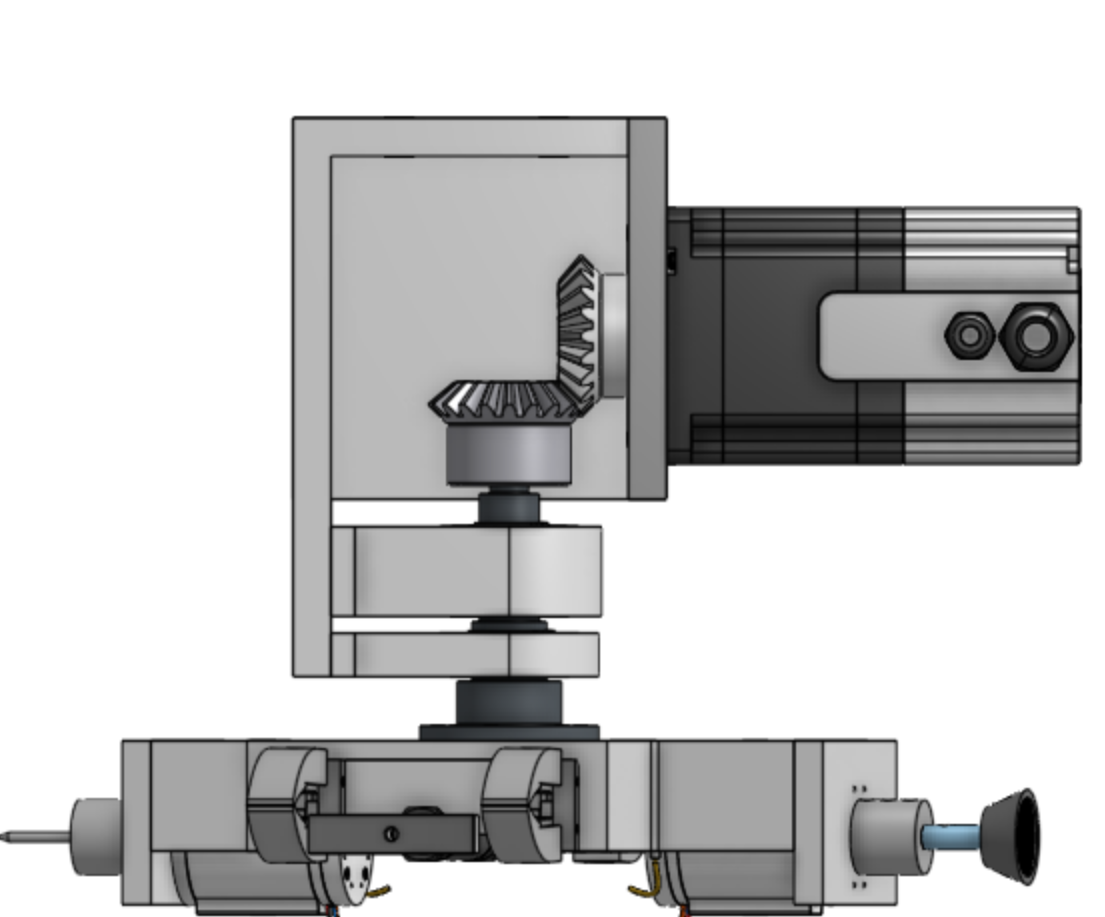
Both tool wheels cycle rapidly between end-effectors via a bevel gear-driven axle, which is mated to the rear of the wheel housing. This provides the necessary rigidity for machining operations, reducing axial play and backlash, while allowing for efficient tool changes to keep cycle times within required parameters.
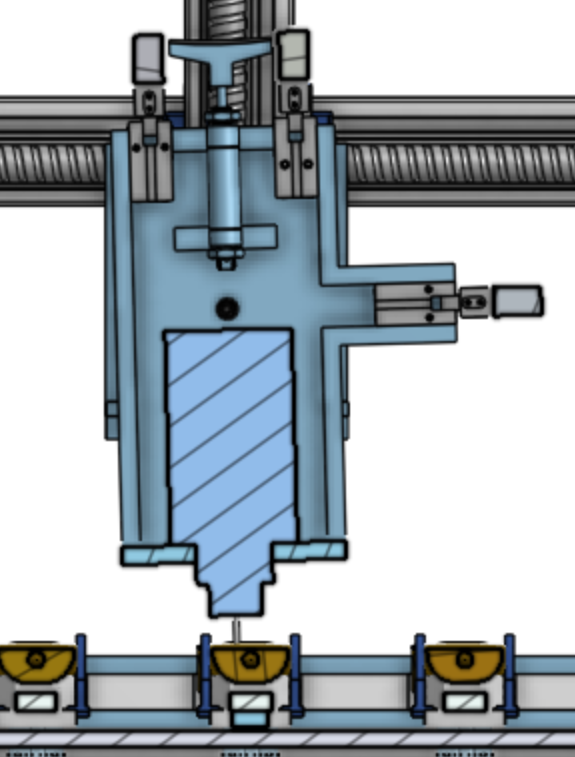
A section-view of the Top Tool Wheel (V1) performing fret slot milling.
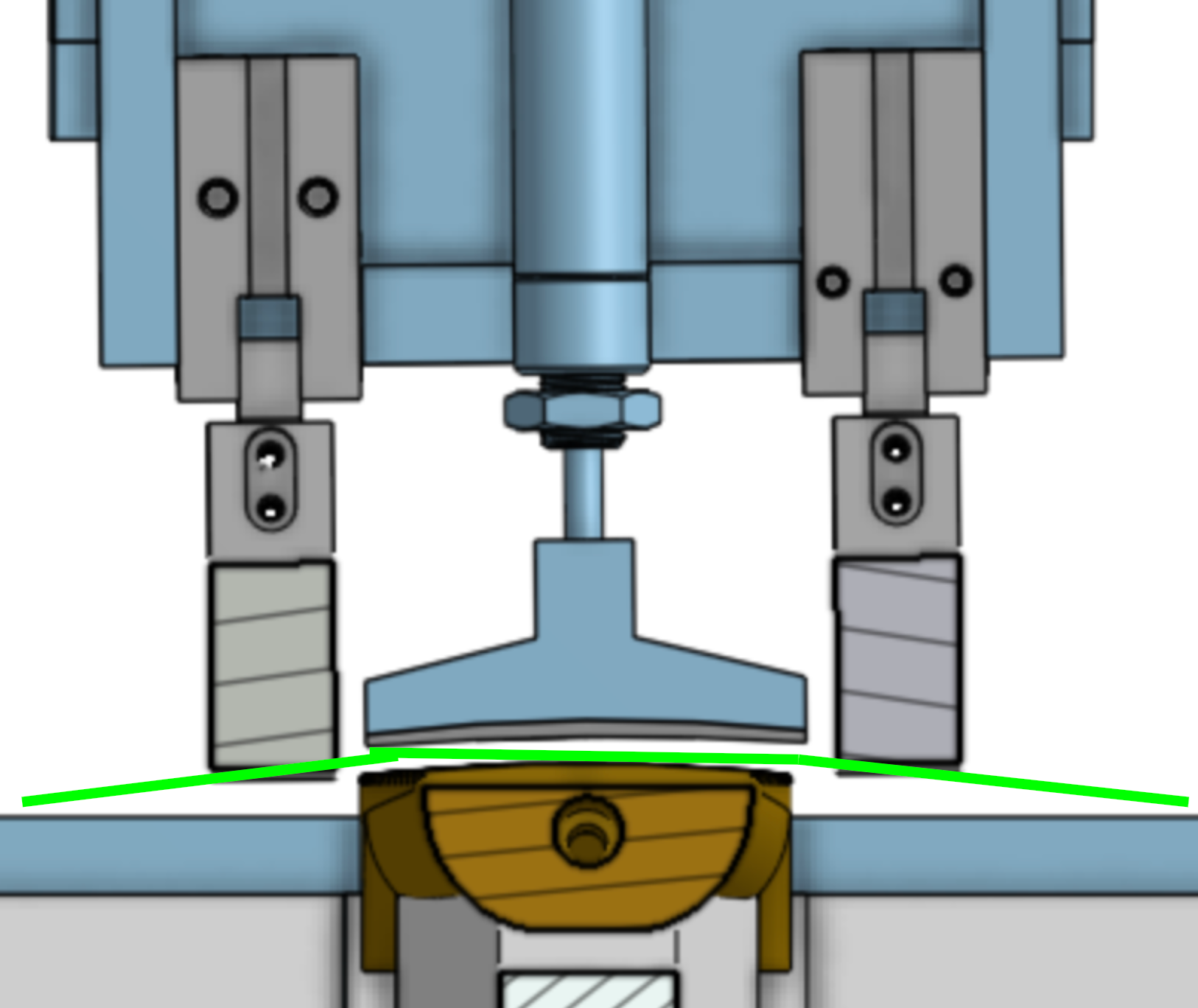
A section-view of the Top Tool Wheel performing fret wire pressing.
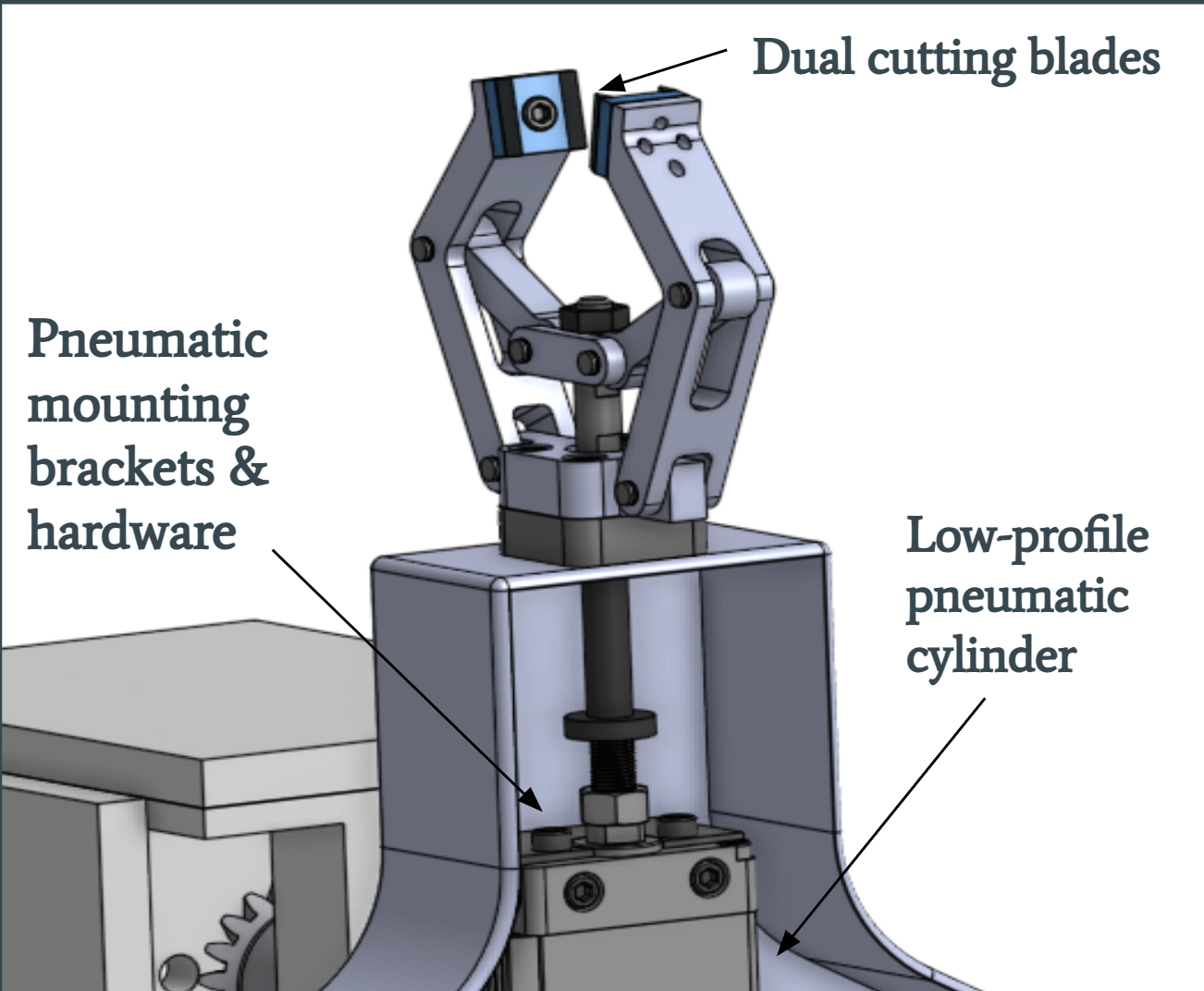
A detail view of the Bottom Tool Wheel's fret cutting end-effector, and the low-profile pneumatic cylinder that drives the cutting mechanism.
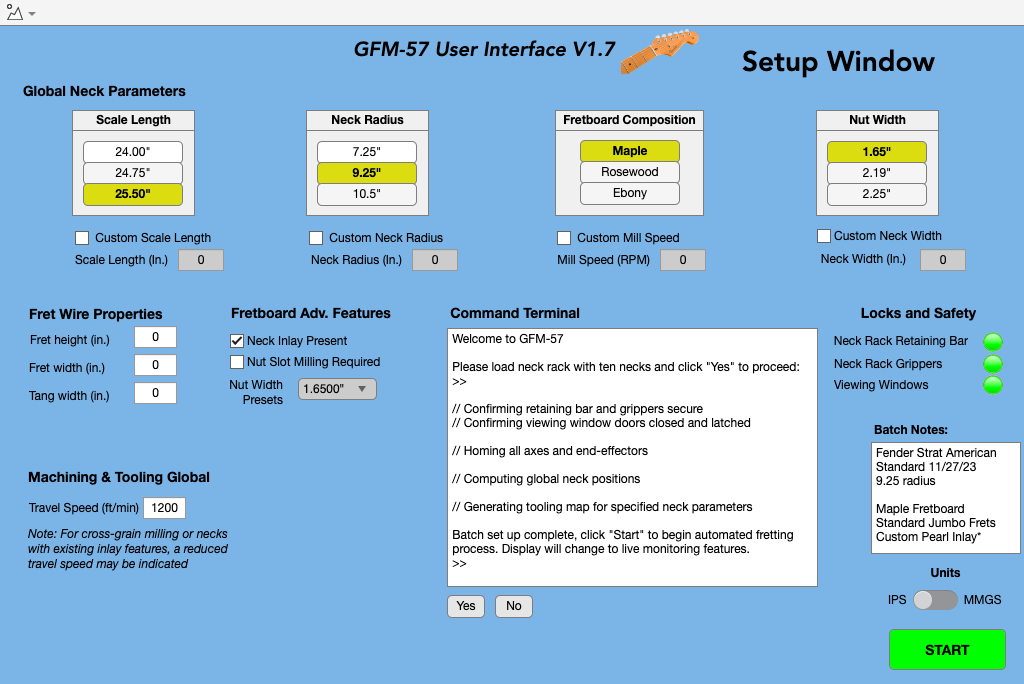
Page 1 of the GUI prompts the user to input the global neck parameters (scale length, radius, fretboard composition, and nut width), in addition to other inputs relating to fret wire properties, optional neck inlay and nut slot milling, and travel speed.
It also includes indicators that track the state of various locking and safety mechanisms.
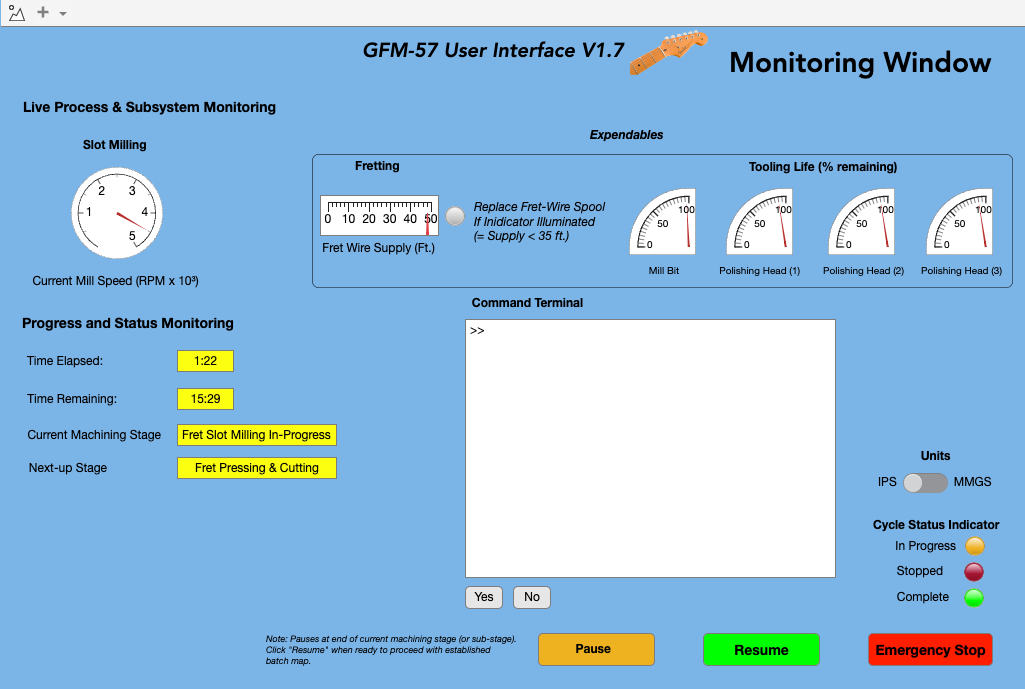
Page 2 of the GUI is for monitoring. It features indicators displaying mill spindle speed, and a dedicated panel for tracking supply of expendables, which include fret wire supply, as well as remaining tooling life for abrasive tool heads. Lastly, it displays the current time elapsed for a batch, remaining time, and current and next-up machining stages.
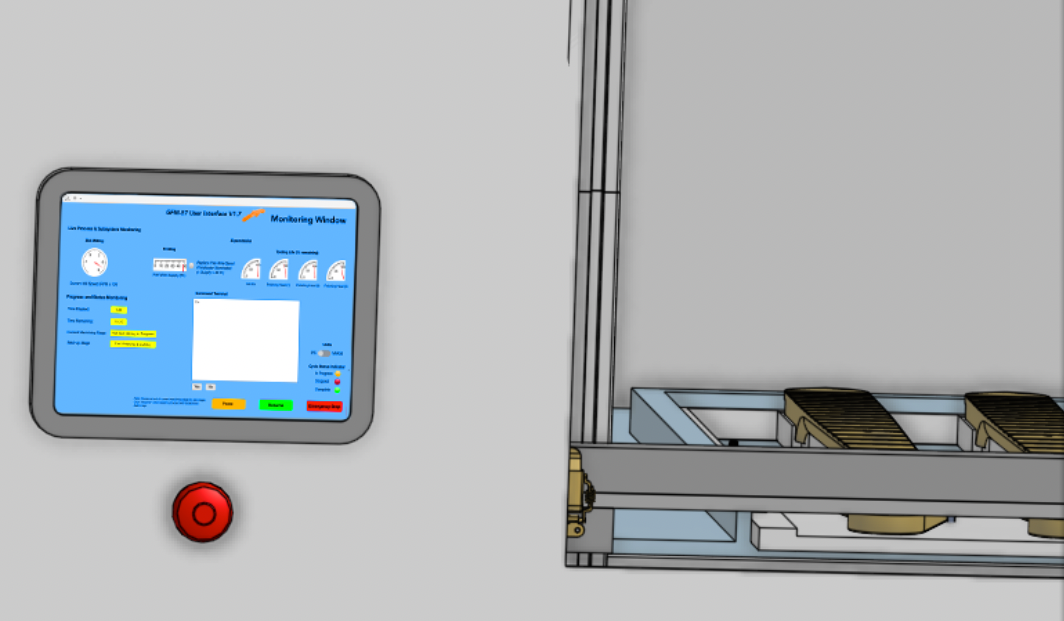
Rendering of GUI displayed on touch screen operator interface.
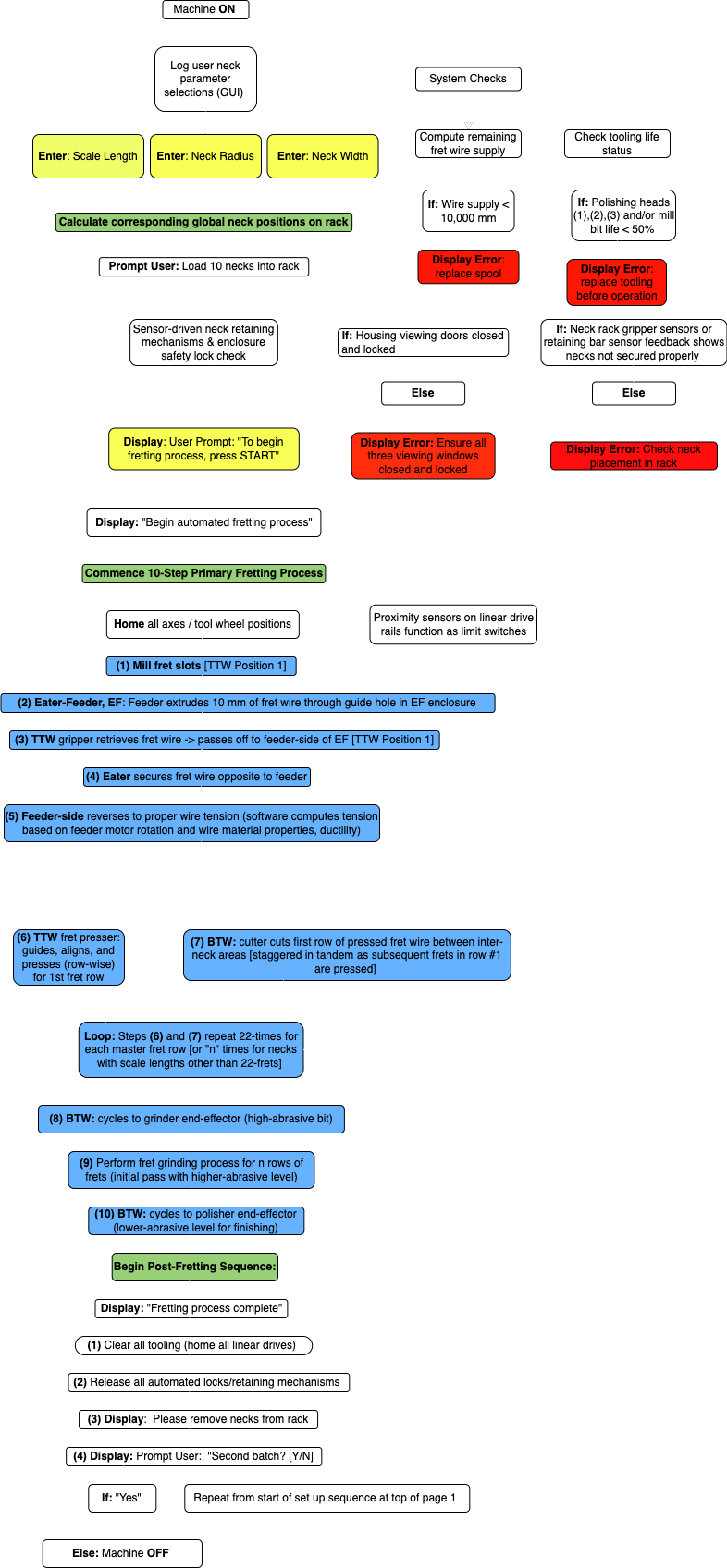

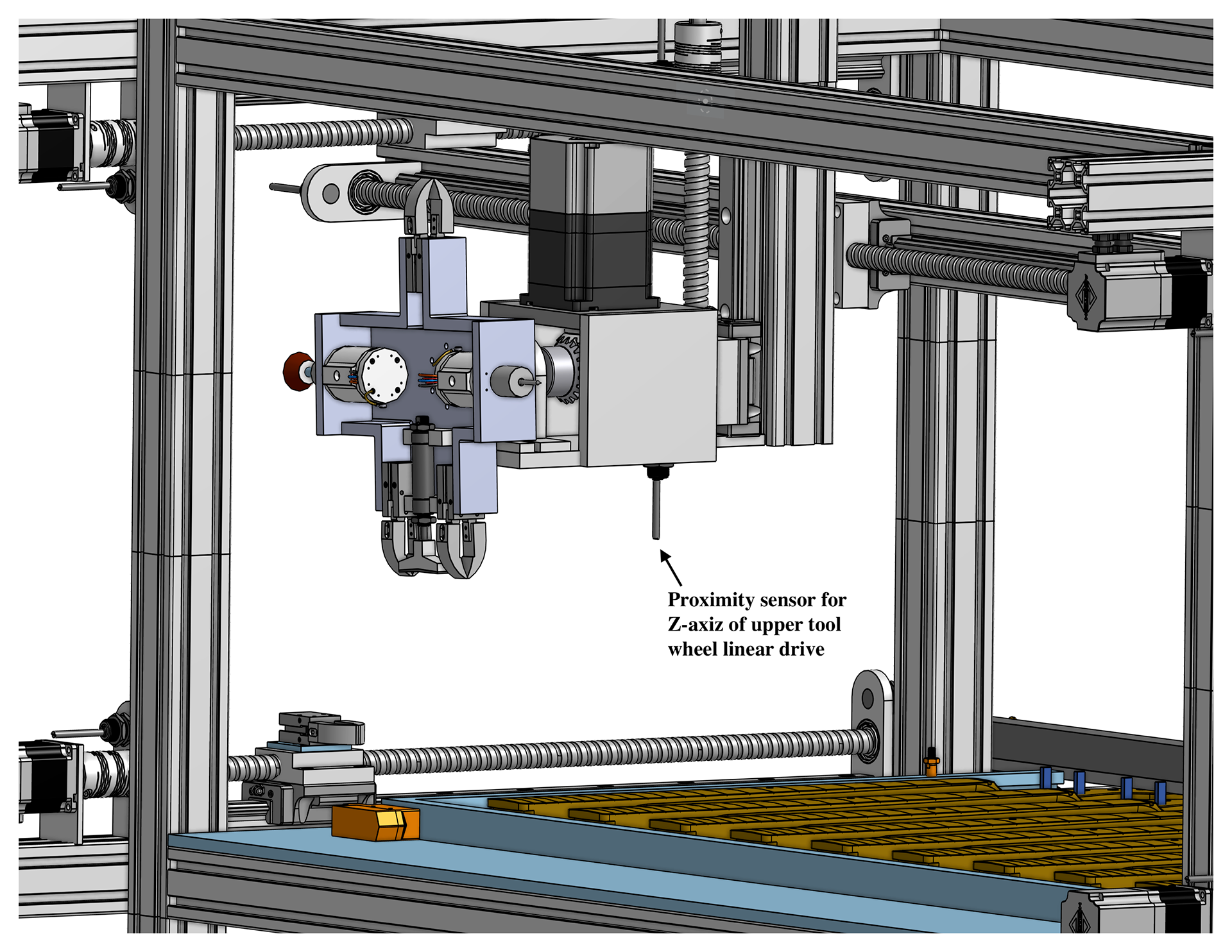
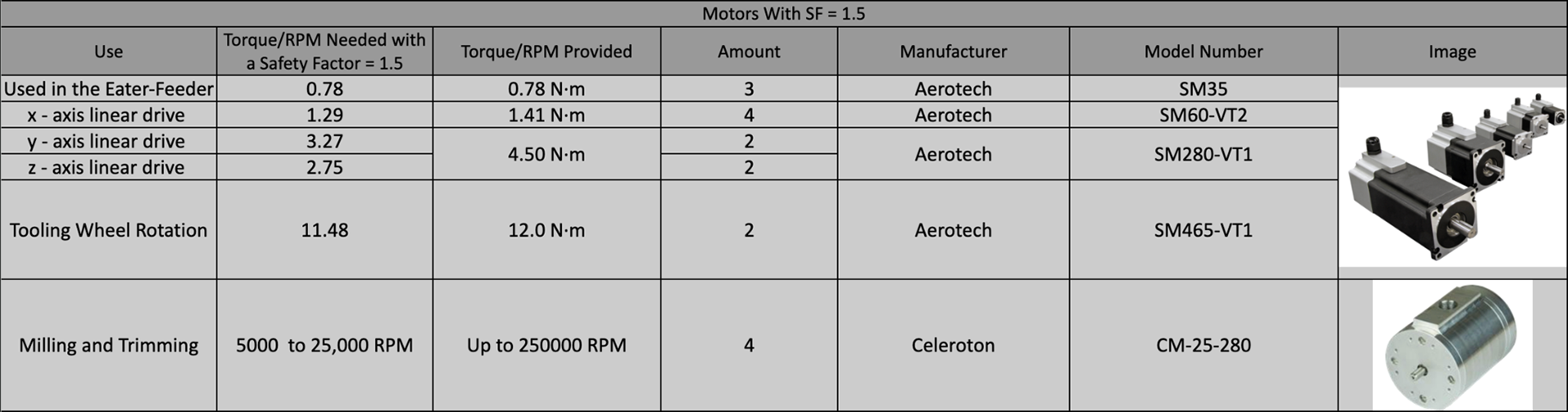
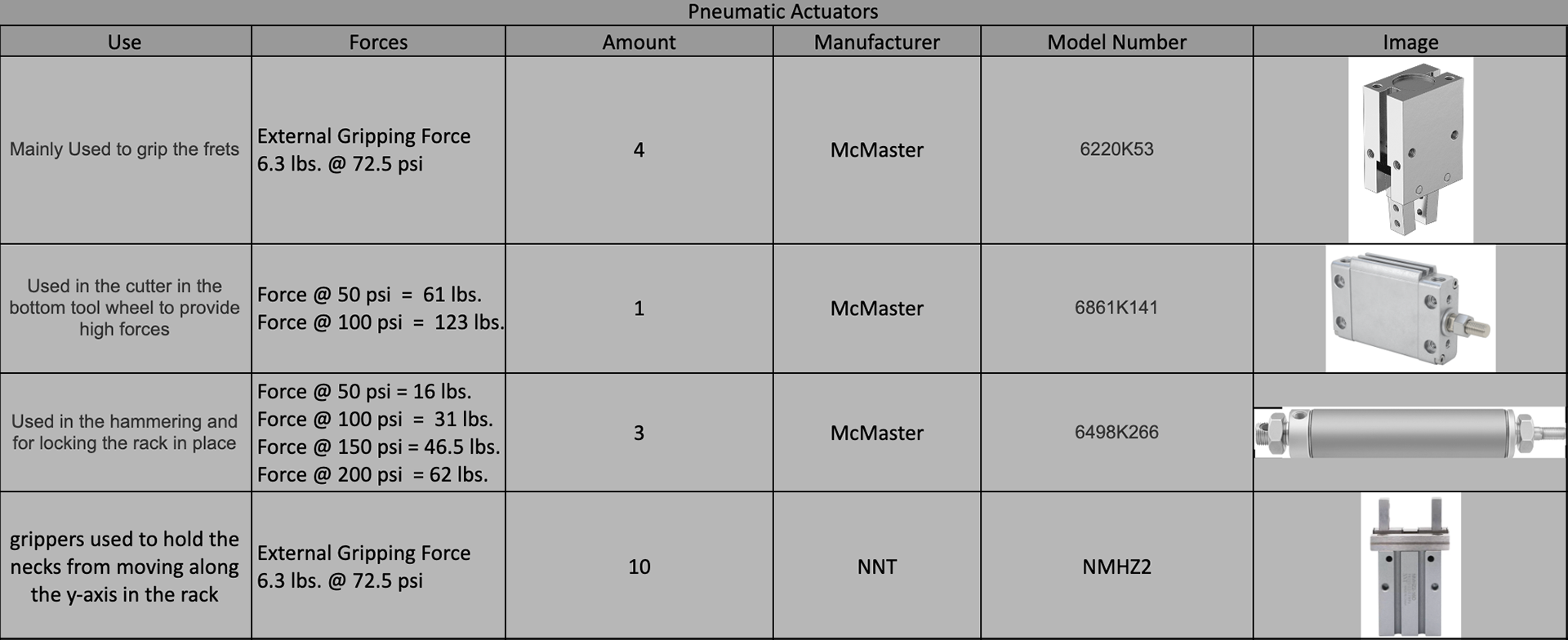